The Aggregate Planning Problem •Given the demand forecast for each period in the planning horizon •Determine the production level, inventory level, and the capacity level for each period that maximizes the firm's (supply chain's) profit over the planning horizon •Specify the planning horizon (typically 318Aggregate Planning Combines appropriate resources into general terms Part of a larger production planning system Disaggregation breaks the plan down into greater detail Disaggregation results in a master production schedule Aggregate Planning Strategies 1 Use inventories to absorb changes in demand 2 Accommodate changes by varyingIn order to satisfy changes in customer demand, the firm must raise or lower inventory levels in anticipation of increased or decreased levels of forecast demand

Aggregate Planning Chapter 11 Mis 373 Basic Operations Management Ppt Download
Level capacity strategy aggregate planning
Level capacity strategy aggregate planning-With a beginning annual inventory of 600 and an ending annual inventory of 600, which set of values are correct for a Level Capacity aggregate planning strategy within Solution andChapter 13 Aggregate Planning 13 1 Menu About us;
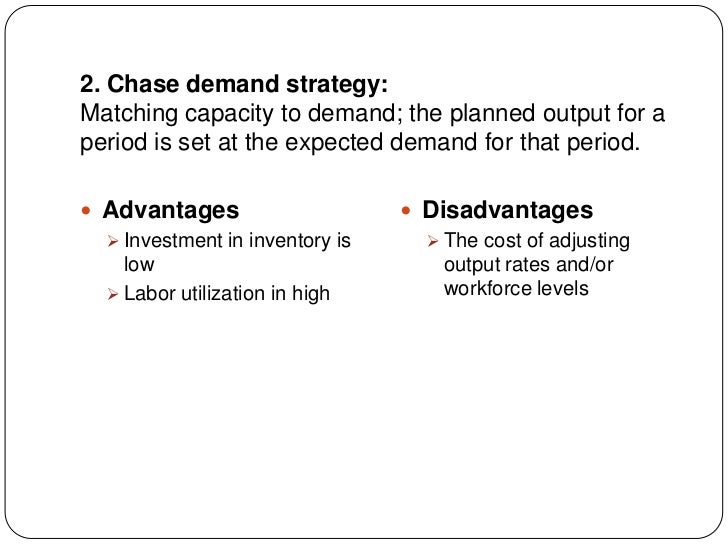



Aggregate Planning Report
Intermediate range capacity planning, Aggregate Capacity The process of planning and managing the overall capacity of an organization's resources Level Capacity Strategy Pure Maintaining a steady rate of regular time output while meeting variations in demand by a combination of opinionWhen using a "level capacity strategy" or "level production strategy" in aggregate planning, variations in demand are met by using which of the following options?Aggregate Planning • Aggregate planning is a part of larger production planning system;
Strategic Capacity Planning Aggregate Planning Long Range Medium Range Short Range How much & when to produce Aggregate Production Planning/ Four General Strategic Plans 1 Level – constant workforce/production level – fluctuating inventory levels 2 Chase – production and manpower fluctuate 3Aggregate planning is capacity planning for a the long range b the intermediate range c the short range d typically one to three months e typically one or more years B The main disadvantage (s) of informal techniques used for aggregate planning is (are) aAs Mixed Strategies Demand and Capacity Options Demand Options The four common demand options primarily focus on market aspects apart from backorders which is strictly operational management in nature The operations manager should know all four demand options but should be more interested in back order option
Chapter 7 Capacity Planning and Management Learning Outcomes After reading this chapter you should be able to • Define and measure capacity and appreciate the factors that influence it • Assess the difficulties of matching capacity to demand • Evaluate and apply the different strategies for matching capacity with demand in the short,The use of a level strategy means that a company will produce at a constant rate regardless of the demand level In companies that produce to stock, this means that finished goods inventory levels will grow during low demand periods and decrease during high demand periodsA level strategy seeks to produce an aggregate plan that maintains a steady production rate and a steady employment level ?
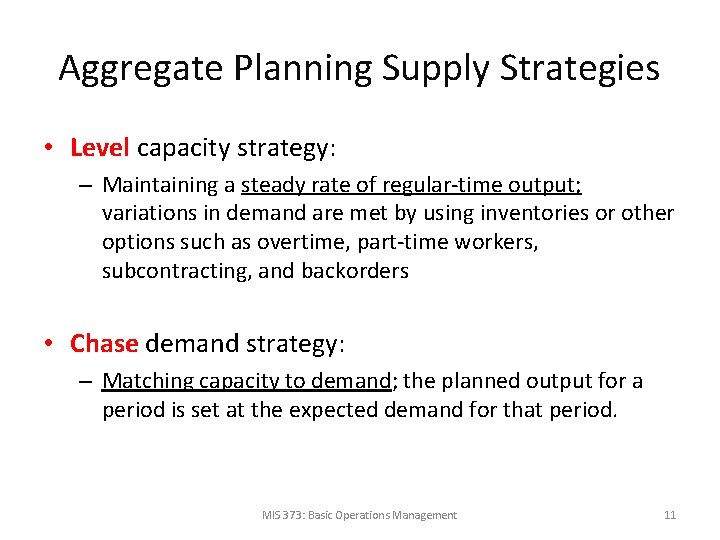



Aggregate Planning Chapter 11 Aggregate Planning Aggregate Planning



Aggregate Planning Mps Capacity Planning Strategic Management Inventory
The primary difference among the three strategies is the lever, that is, the parameter that is manipulated to achieve equality of supply and demand over the aggregate planning period The first chase strategy uses capacity, in the form of machine or personnel capacity, as the leverHowever, it is feasible to hire or lay off workers, increase or reduce the work week,Capacity and Aggregate Planning Aggregate Planning The process




Pdf Analysis Of Aggregate Planning For Development Strategy Case Study Of Gasoline Distribution Company In Indonesia Semantic Scholar
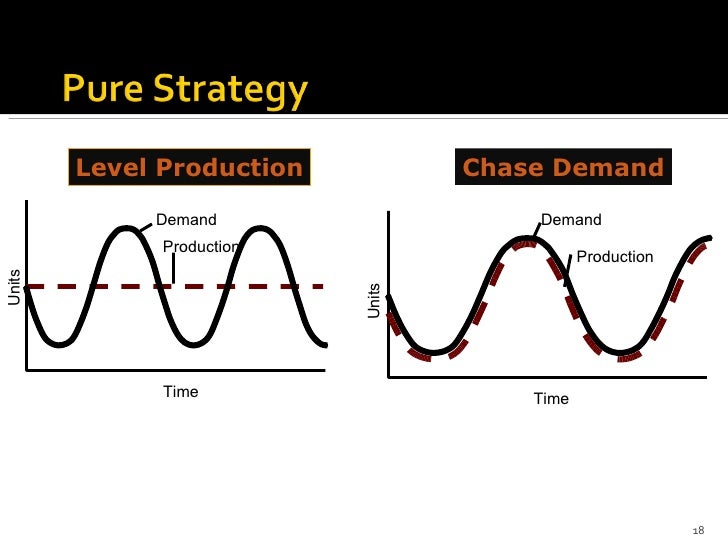



Productionplanning Aggregate Capacity
Taking plans from the aggregate level, disaggregate planning generates a general plan of action that will help the firm prepare for upcoming production The WIP/quota setting problem decides the quantity of work in process or periodic production quotas according to aggregate plan and capacity's characteristics (eg, setup time, changeover time among batches, productionI varying output during regular time without changing workforce size (for example, using overtime) II Varying output during regular time by changing workforce size IIIRole of Aggregate Planning in a Supply Chain Basic Assumptions – Capacity has a cost – Lead times are greater than zero Aggregate planning – Is the process by which a company determines levels of capacity, production, subcontracting, inventory, stockouts, and pricing over a specified time horizon – goal is to maximize profit Or, if



Sustainability In Supply Chain Management Aggregate Planning From Sustainability Perspective
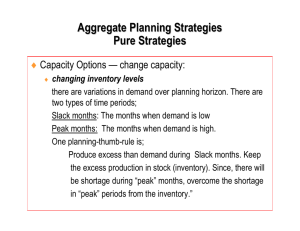



Chapter 13 Aggregate Planning
Aggregate production planning (APP) determines the resource capacity a firm will need to meet its demand over an intermediate time horizonsix to twelve months in the future Within this time frame, it is usually not feasible to increase capacity by building new facilities or purchasing new equipment; Level Strategy • Level strategy is a strategy the firm maintains a constant capacity over a period of time irrespective of the fluctuations in demand • This strategy is used when the skill level, training required, or the cost of hiring people and terminating them is high Demand Units Time Production 7 8 The aggregate planning that we are going to carry out will among other things attempt to match the level of bike supply to demand It is going to determine the required quantities and the timing of inputs as well as outputs There will also be making decisions on production, inventory, staffing and backorder levels




Aggregate Planning 101 What You Need To Know Brendan Jones




Operations Management Aggregate Planning Chapter Ppt Video Online Download
Maximize utilization of plant and equipment Aggregate Production Planning (APP) Operations Managers try to determine the best way to meet forecasted demand by adjusting various capacity Aggregate Planning balancing demand/capacity Strategies for meeting uneven supply & demand Level capacity maintain a level (steady rate) of production Capacity planning is a strategic process whereby a company determines what level of capacity it will need to satisfy the level of demand forThe Extremes Level Chase Strategy Strategy Production Production rate equals is constant demand Basic Aggregate Planning Strategies for Meeting Demand Level capacity strategy • Keeping work force constant and maintaining a steady rate of regulartime output while meeting variations in demand by a combination of options (such as using inventories overtimeparttime
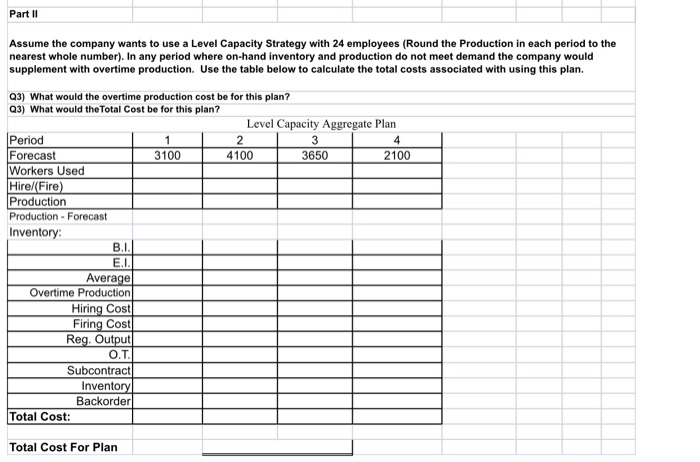



Solved Part Ii Assume The Company Wants To Use A Level Ca Chegg Com
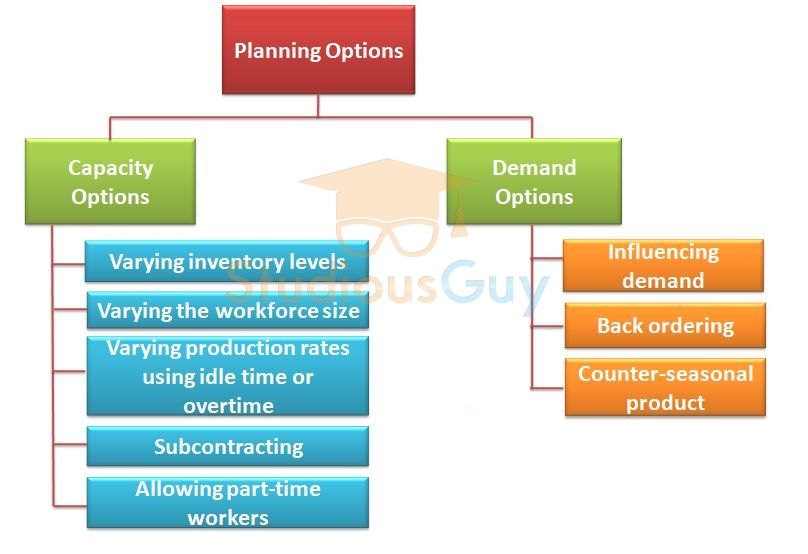



Aggregate Planning Studiousguy
DMCA / Copyright Policy;DMCA / Copyright Policy;In this lesson, we investigate the process of developing a level production plan in this aggregate planning segment
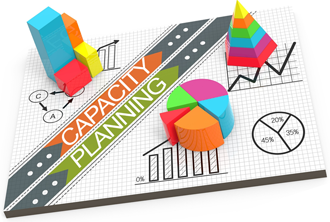



Capacity Planning Meaning Classification And Its Goals



1
Steps involved in aggregate capacity management Understanding the aggregate demand and supply for a specific period of time Preparation of suitable plans and contingency plans for situations where the demand levels might fluctuate Finalizing an appropriate planAggregate planning strategies Implementing aggregate planning in practice 2 Role of Aggregate Planning Capacity has a cost, lead times are greater than zero Atli Aggregate planning process by which a company determines levels of capacity, production, subcontracting, inventory, stockouts, Aggregate planning is a marketing activity that does an aggregate plan for the production process, in advance of 6 to 18 months, to give an idea to management as to what quantity of materials and other resources are to be procured and when, so that the total cost of operations of the organization is kept to the minimum over that period
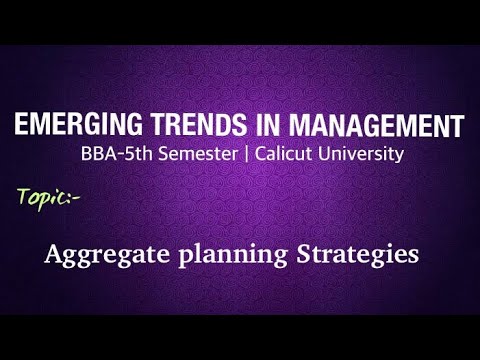



Aggregate Planning Strategies Chase Strategy Capacity Strategy Level Strategy a 5th Sem Cu Youtube



Http Www1 Pu Edu Tw Ylai Erp Dom 1042 Ppts S16 1042 Erp Dom Ap S16 Pdf
Aggregate planning is a type of medium range capacity planning that typically covers a 3 to 18 month period of time Used in a manufacturing environment and determines overall output levels planned as well as appropriate resource Reactive Aggregate Planning Strategy The reactive aggregate planning strategy helps in managing fluctuating project demands through different plans The reactive aggregate planning strategy creates changes in the capacity to match with the changing demand Here are options widely used when developing the reactive aggregate planning strategyAggregate Planning Strategies Tradeoff between capacity, inventory, backlog/lost sales Chase strategy – using capacity as the lever Time flexibility from workforce or capacity strategy – using utilization as the lever Level strategy – using inventory as the lever Tailored or hybrid strategy – a combination of strategies



Sihombing15 Files Wordpress Com 08 08 Ch 7 Aggregate Capacity Planning Pdf
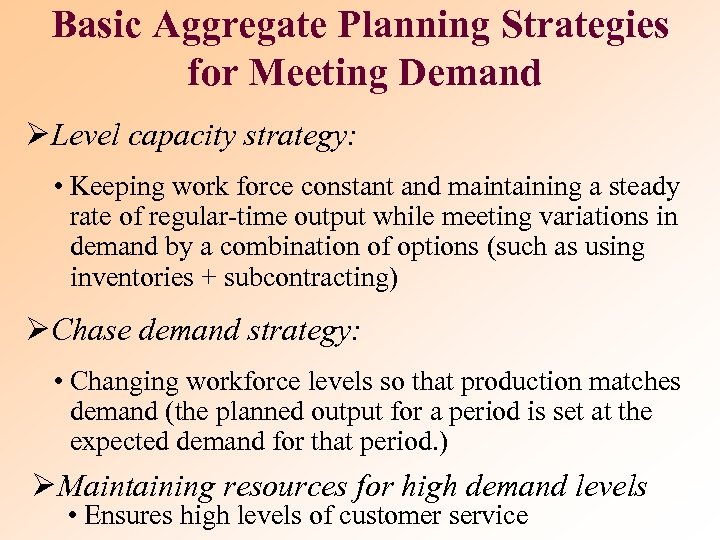



Aggregate Planning Planning Horizon Aggregate Planning Intermediate Range
Strategic Network Planning Master Planning Distribution Planning Transport Planning Production Aggregate Planning a Level Work Force Plan `backorders allowed Aggregate Planning Available capacity 50 50 10 12 14 16 0 350 150 50 75 75 0 300 300About Press Copyright Contact us Creators Advertise Developers Terms Privacy Policy & Safety How works Test new features Press Copyright Contact us Creators There are two main aggregate planning methods and strategies the chase strategy and level strategy The chase strategy sets production equal to forecasted demand Many service organizations such as schools, hospitality businesses and hospitals, use the chase strategy The level strategy is mainly focused on maintaining a constant output rate




Production Planning Control Chapter 2 Aggregate Planning Master Production Scheduling Chapter2 1 Pdf Free Download
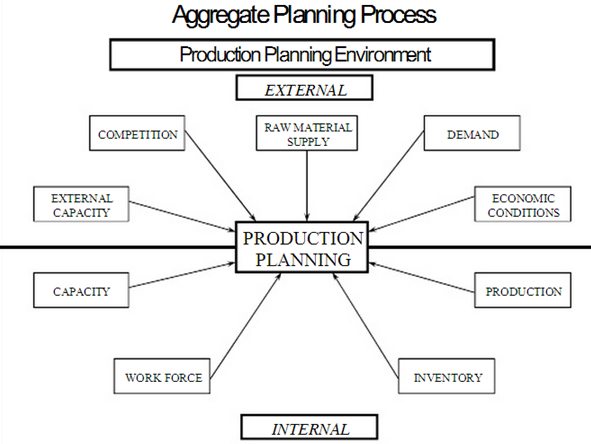



Aggregate Production Planning Aggregate Planning Process Aggregate Production Planning Strategies
• Different aggregate planning strategies & options for changing demand and/or capacity in aggregate plans • Develop aggregate plans, calculate associated costs, and evaluate the plan in terms of operations, marketing, finance, and human resources • Differences between aggregate plans for service and manufacturing companiesLevel scheduling maintains a constant output rate, production rate, or workforce level over the planning horizon In other words, a level strategy is an aggregate plan in which production is uniform from period to period Firms like Toyota and Nissan keep production at uniform levels and may (1) let the finished goods inventory go up or down toLevel capacity strategy When an organization adopts the level capacity strategy then it manufactures at a constant output rate It does not consider any fluctuation or change in the level of demand This may lead to stockpiling or holding of inventory in high quantity, when there is a decrease in the demand level
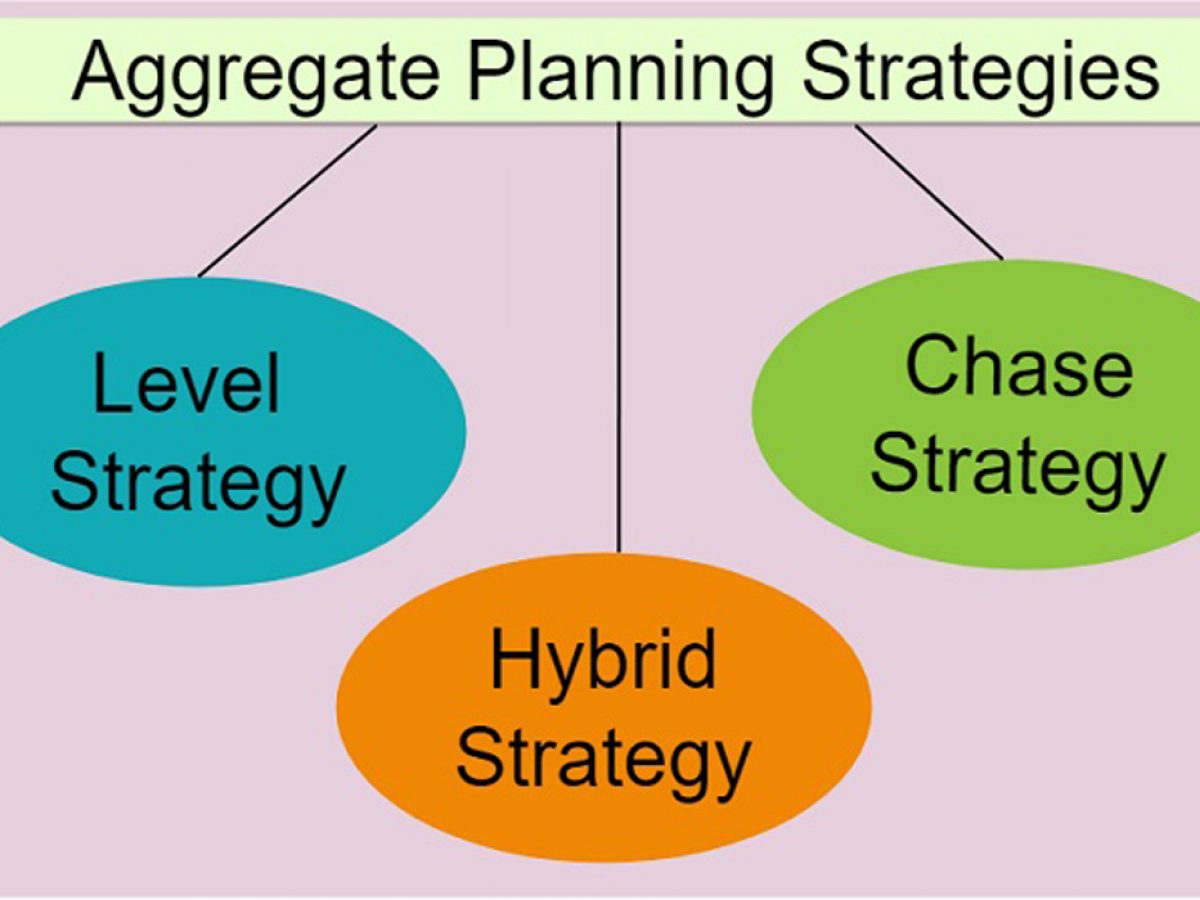



What Is Aggregate Planning 3 Strategies For Aggregate Production Planning
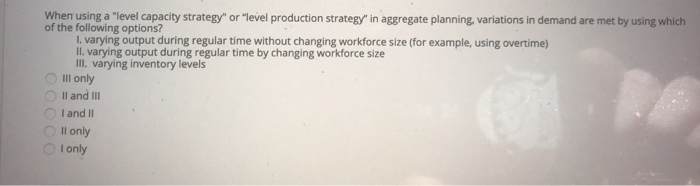



When Using A Level Capacity Strategy Or Level Chegg Com
Inputs and Outputs to Aggregate Production Planning Aggregate Production Planning Demand Forecasts Company Policies Financial Constraints Strategic Objectives Capacity Constraints Size of Workforce Production per month (in units or $) Inventory Levels Units or dollars subcontracted, back ordered, or lost 18Therefore understanding the interfaces between plan and several internal and external factors is essential for effective aggregate planning 8 Capacity planning is defined as a method to gauge the production capacity needed to meet the changing product demands of an organization Two terms of design capacity and effective capacity are used extensively in the context of capacity planning The first is the maximum work that is completed in a specific period by an organization, and the latter is the




Aggregate Planning And Forecasting In Make To Order Production Systems Sciencedirect



Aggregate Planning Strategies Of Scm Inventory Demand
Example 1 Level strategy • Each period is hours • From the beginning manager has 10 parttime workers • She wants to minimize undertime in this level strategy • Maximize overtime in order to minimize undertime • Overtime can not exceed percent of the regular time (that is 4 hour) in any period •



Master Production Schedule
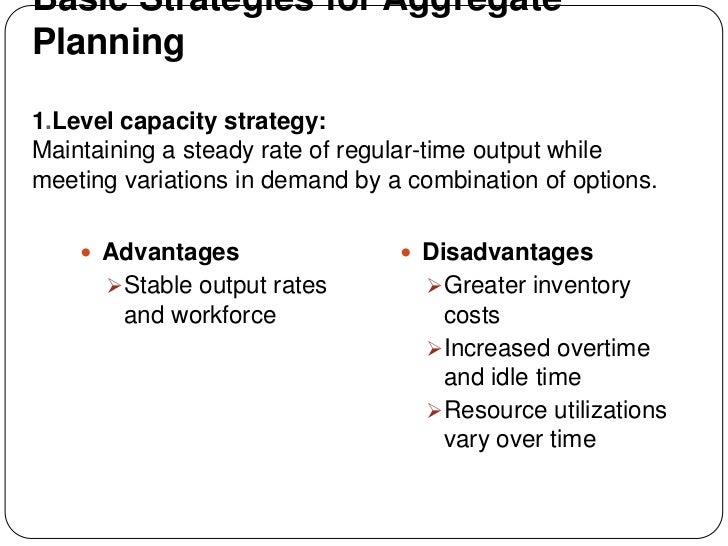



Aggregate Planning Report
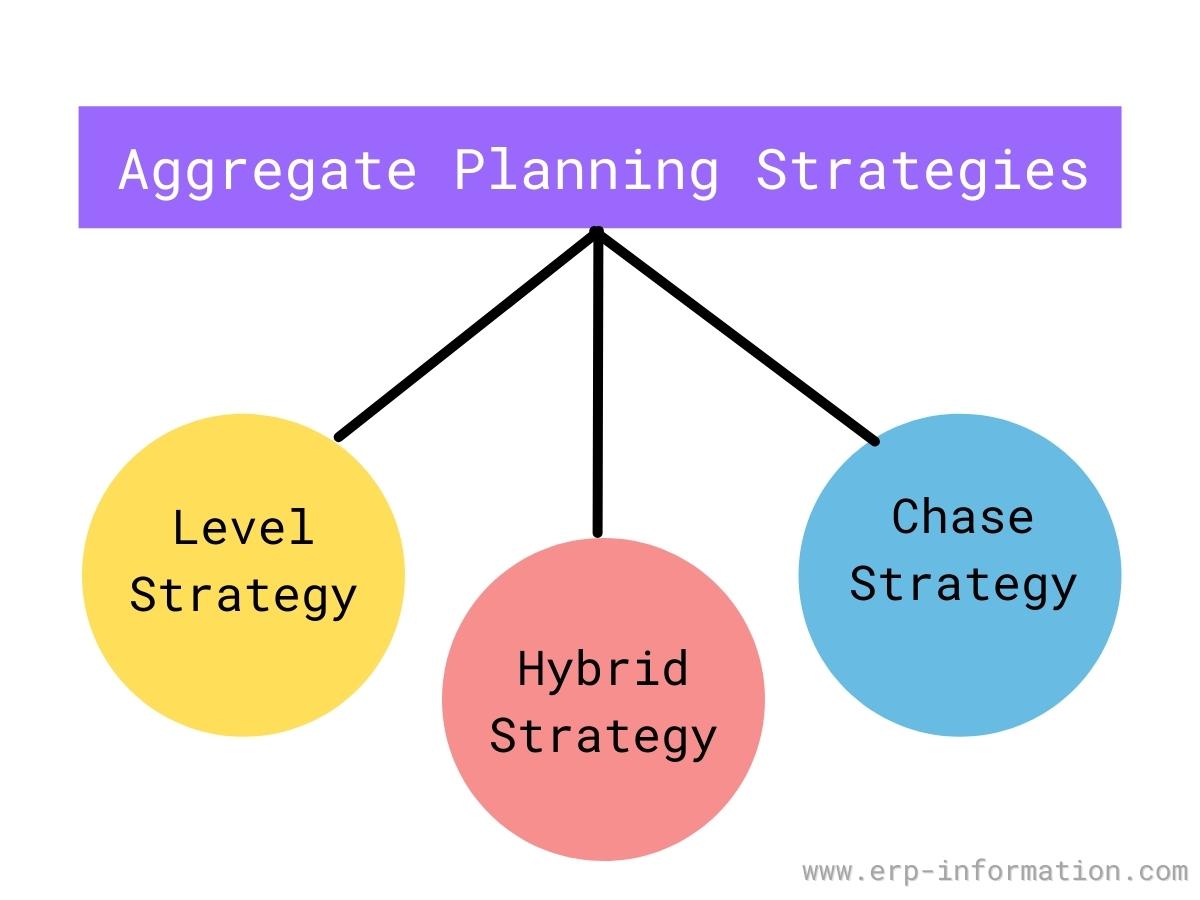



What Is Aggregate Planning 3 Strategies For Aggregate Production Planning




Pdf Aggregate Production Planning For A Pump Manufacturing Company Level Strategy
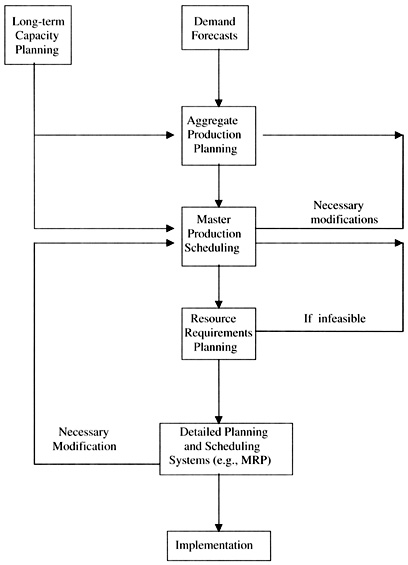



Aggregate Plan And Master Production Schedule Linkage Springerlink



Strategies For Developing Aggregate Plans Assignment Help Aggregate Planning Process




Aggregate Planning Strategy Organization Levels System Examples Model Type Company System



1
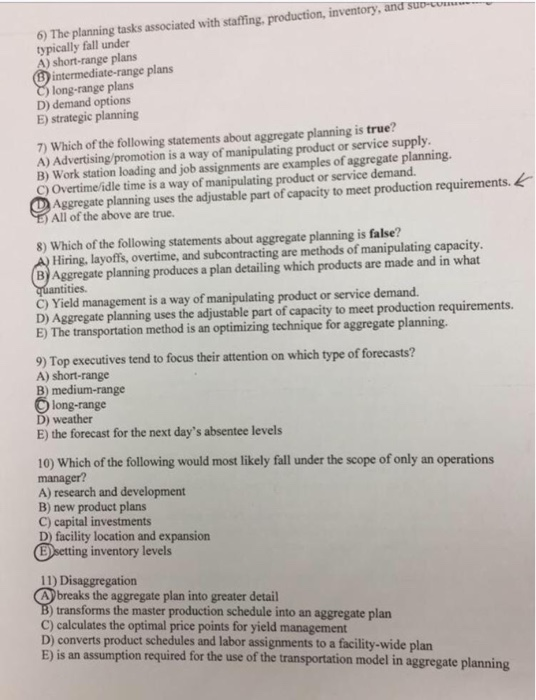



M Which Of The Following Is The Term Used For Medium Chegg Com
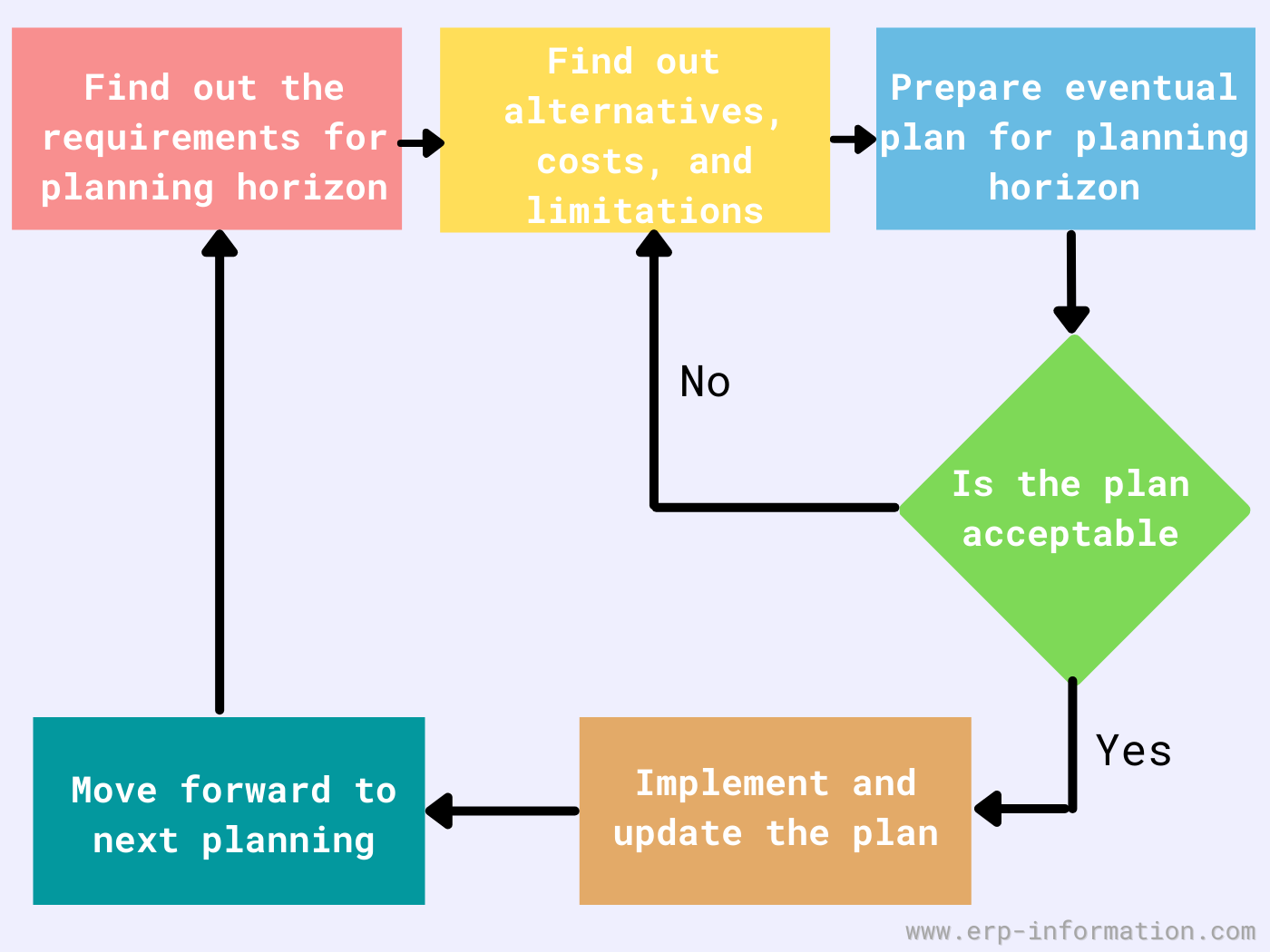



What Is Aggregate Planning 3 Strategies For Aggregate Production Planning
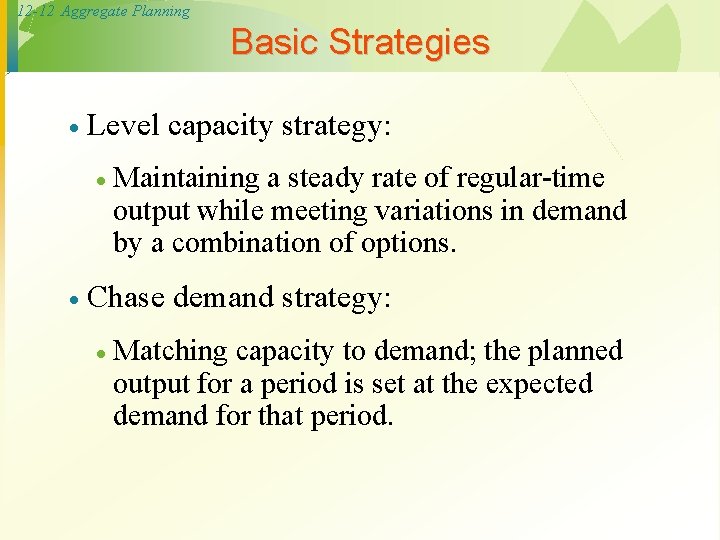



12 1 Aggregate Planning Operations Management William J




Aggregate Planning




Everything About Capacity Planning Strategies Its Benefits




Sap Integrated Business Planning Ibp Sales And Operations Planning 18 Sap Blogs




Aggregate Planning



2




Aggregate Capacity Planning Pdf Free Download
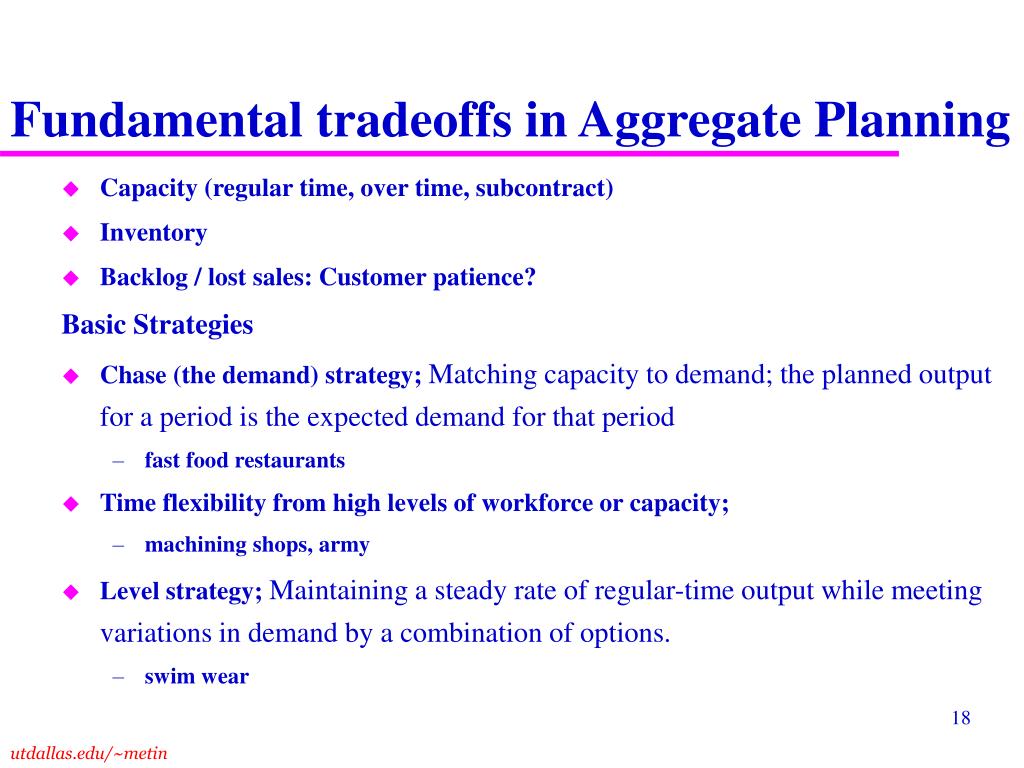



Ppt Aggregate Planning Powerpoint Presentation Free Download Id
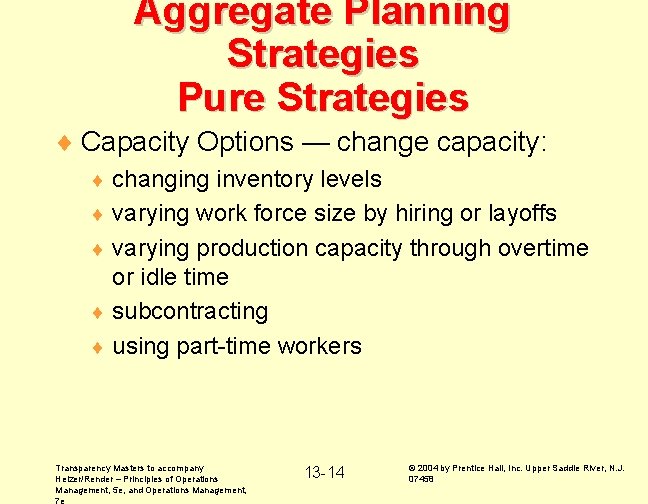



Operations Management Aggregate Planning Chapter 13 Transparency Masters
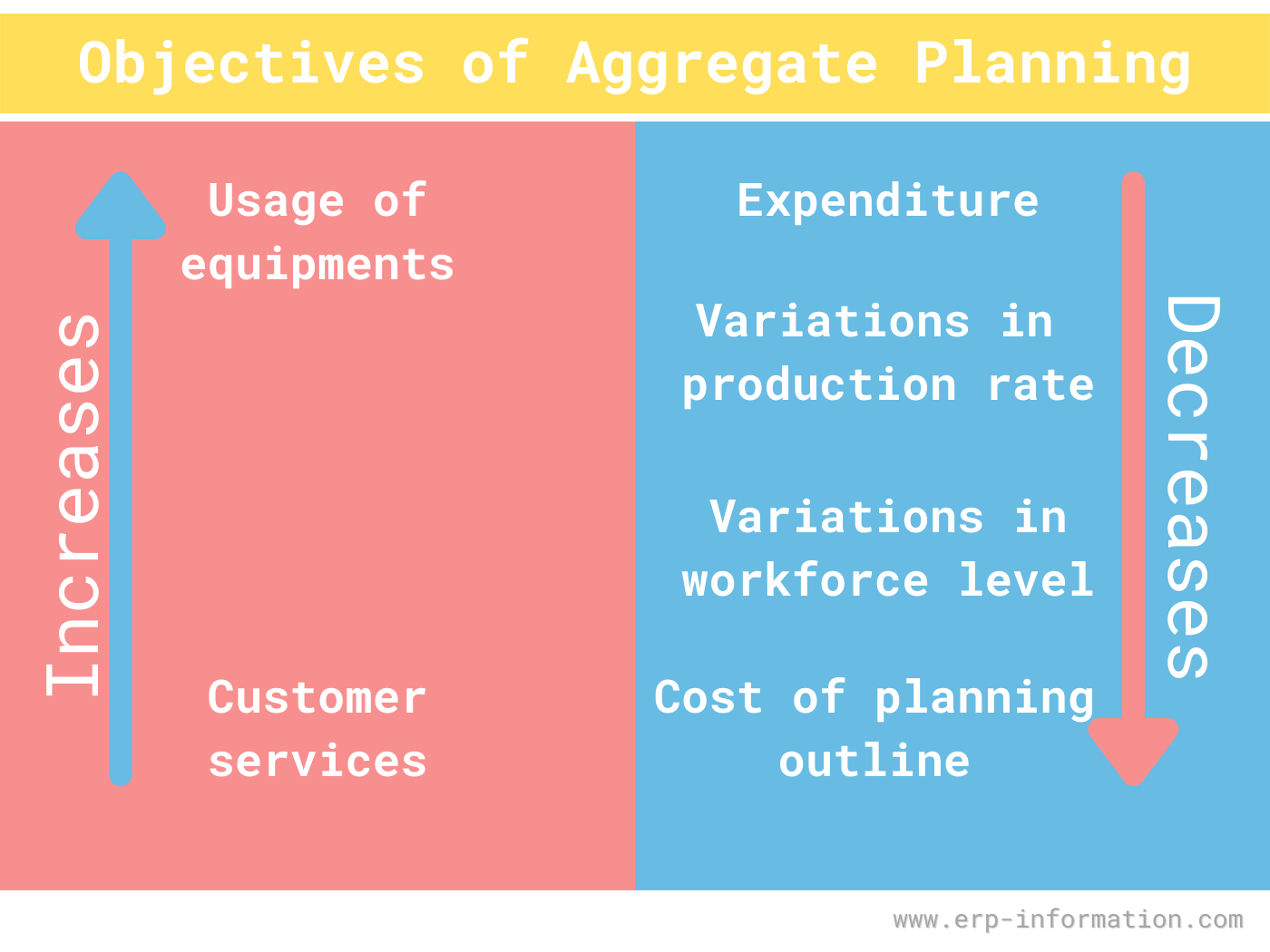



What Is Aggregate Planning 3 Strategies For Aggregate Production Planning



Aggregate Planning
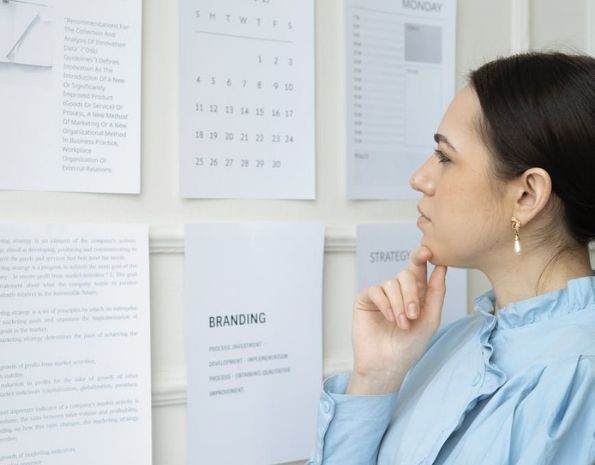



Aggregate Planning Strategies Methods And Examples Harappa Education
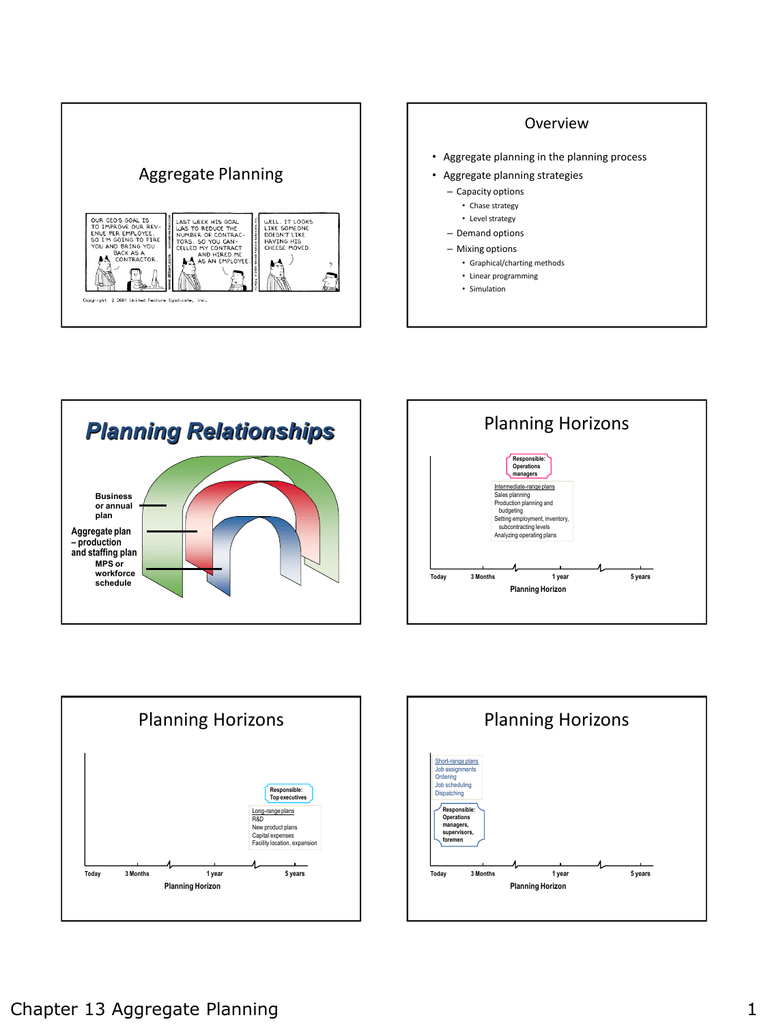



Planning Relationships Planning Horizons Aggregate Planning



Http Www1 Pu Edu Tw Ylai Erp Dom 1042 Ppts S16 1042 Erp Dom Ap S16 Pdf
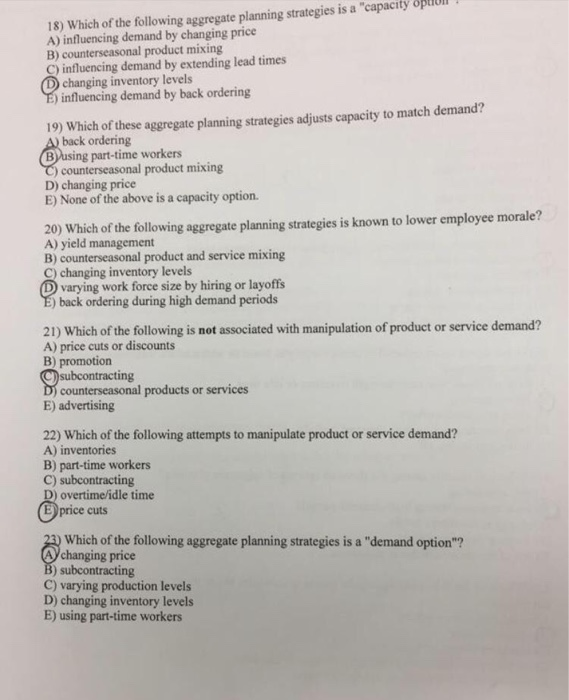



M Which Of The Following Is The Term Used For Medium Chegg Com




Safety Stock In Inventory Systems Depends Only On The Average Demand During The Course Hero




Solved The Owner Of A Small Mill Working Plant That Builds Cabinets Is 1 Answer Transtutors



1



Aggregate Scheduling Handouts Demand Mathematical Optimization




Sales And Operations Planning Aggregate Planning Production Planning Operations Planning How To Meet Effectively And Efficiently Forecasted Requirements Ppt Video Online Download




Which Of These Aggerate Planning Strategies Is A Capacity Option Nadex Cfpb Complaint




Aggregate Planning 101 What You Need To Know Brendan Jones
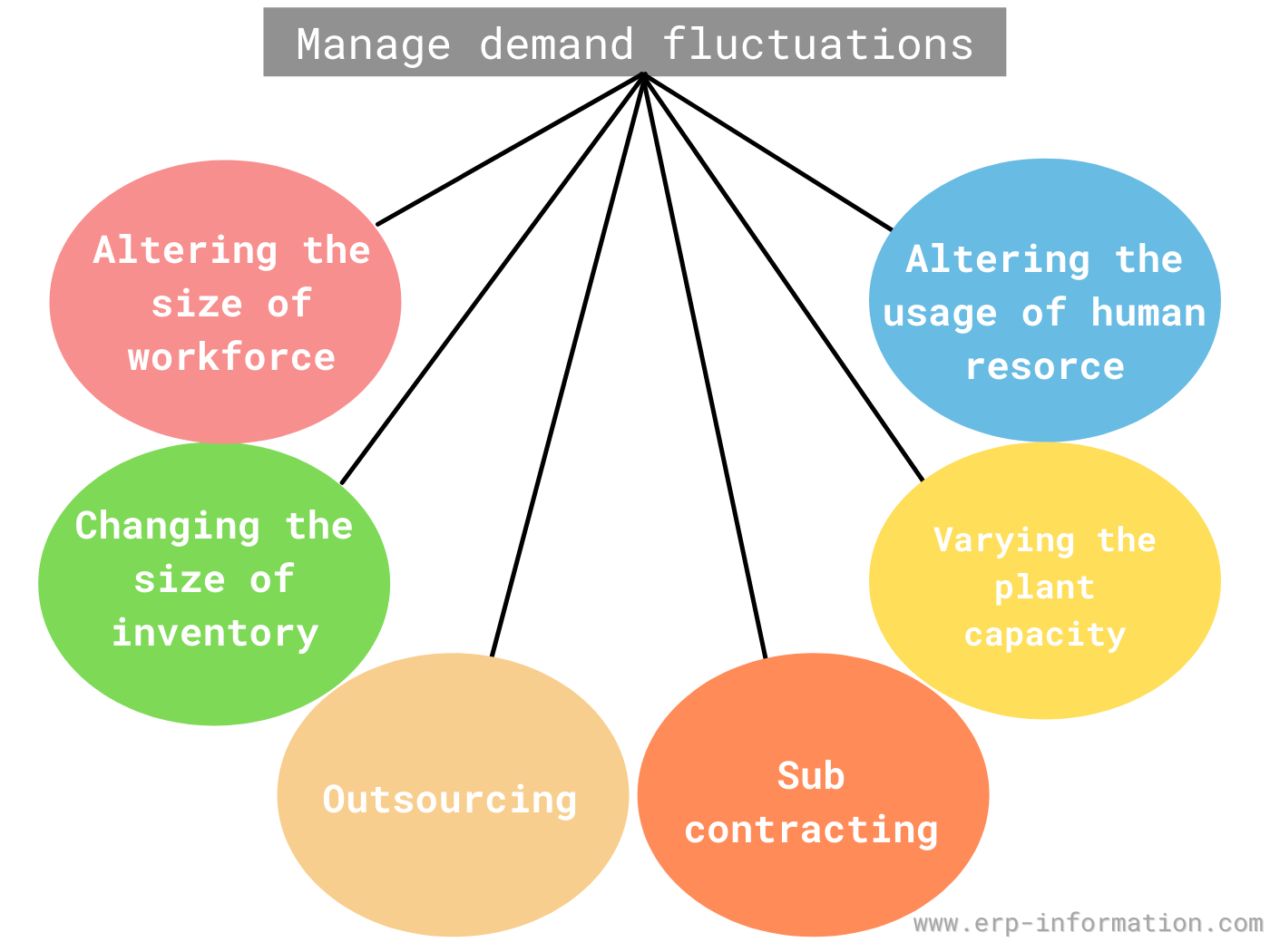



What Is Aggregate Planning 3 Strategies For Aggregate Production Planning
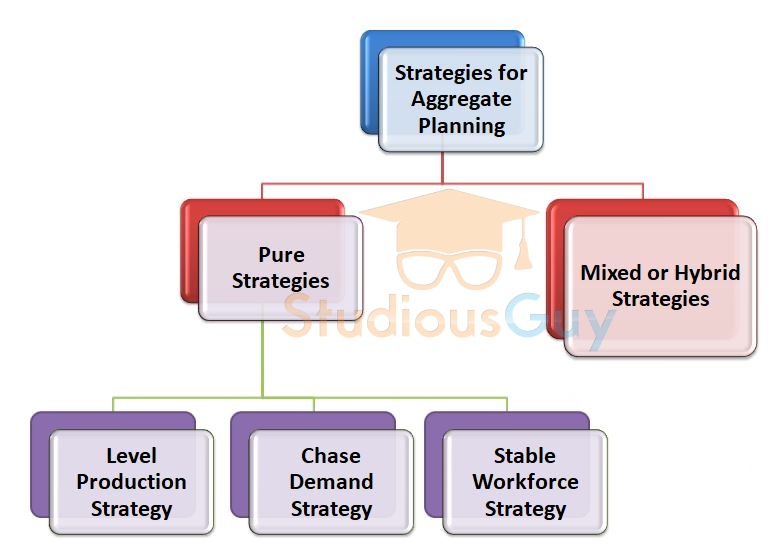



Aggregate Planning Studiousguy
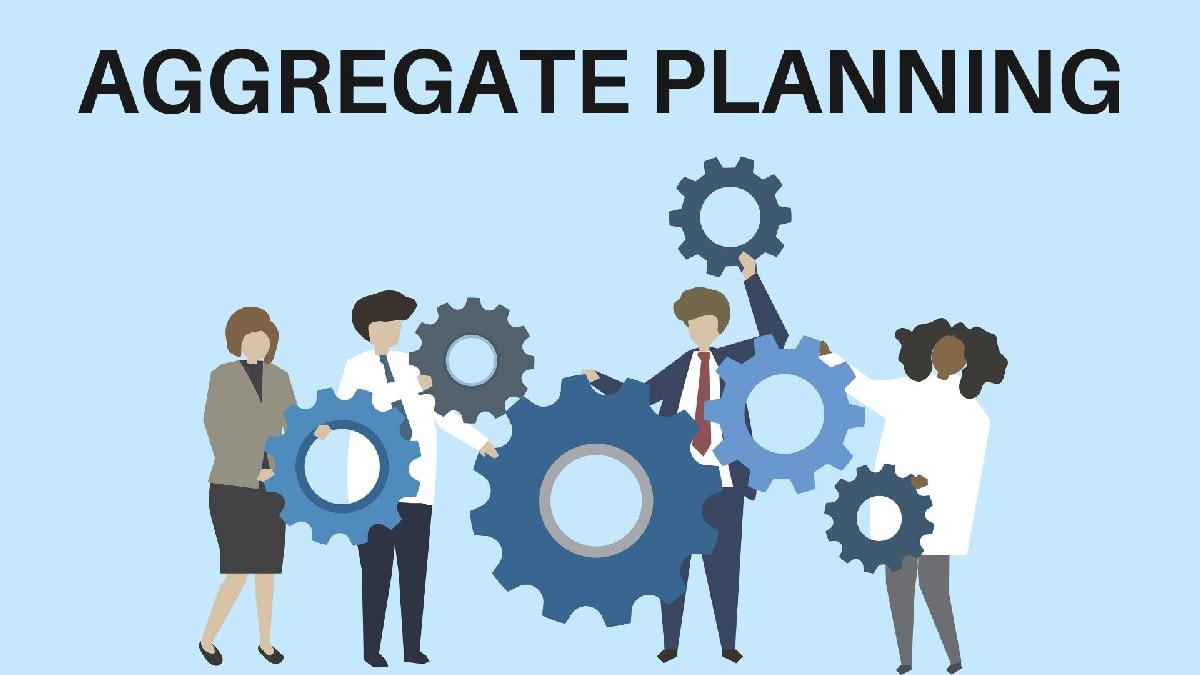



Aggregate Planning Definition Importance Strategies Management And Advantages
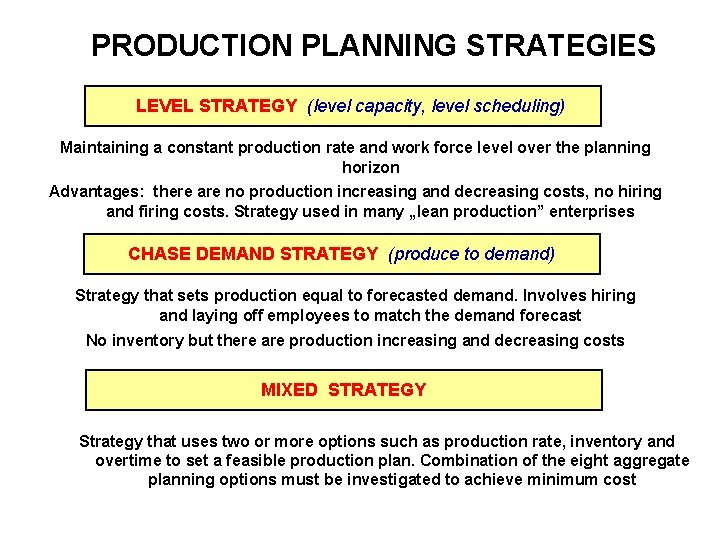



Sales And Operations Planning Aggregate Planning Production Planning



Myclass Dau Edu cswebdav Xid 4 2




Aggregate Planning Chapter 11 Mis 373 Basic Operations Management Ppt Download
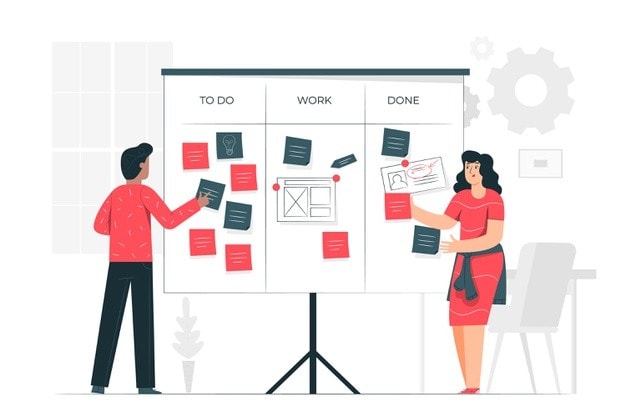



Aggregate Planning Definition Importance Strategies Management And Advantages
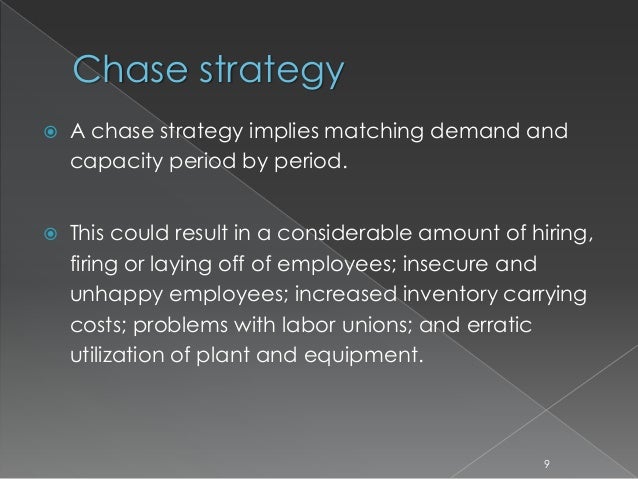



Aggregate Planning
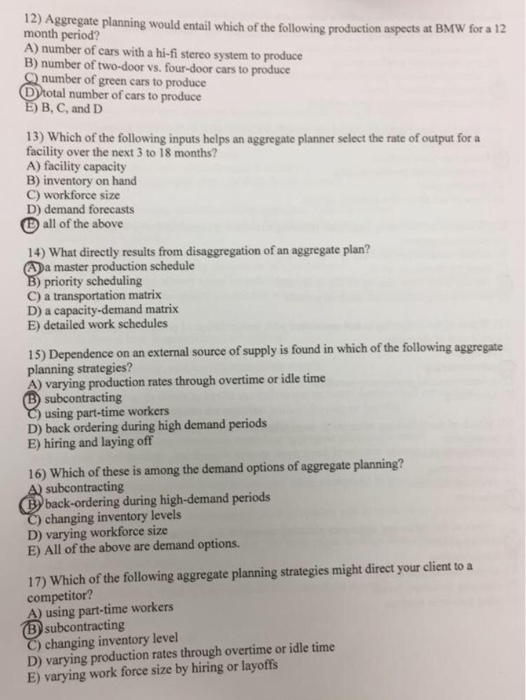



M Which Of The Following Is The Term Used For Medium Chegg Com




1 Dsci 4743 Inputs And Outputs To Aggregate Production Planning Aggregate Production Planning Company Policies Financial Constraints Strategic Objectives Ppt Powerpoint
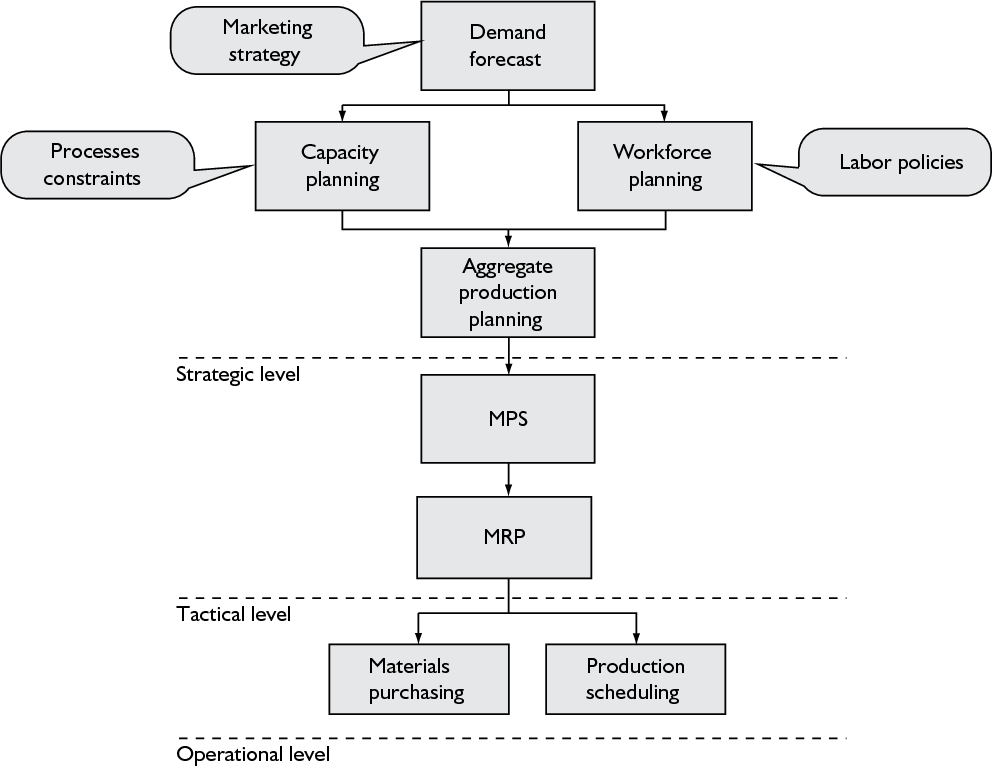



Aggregate Planning For A Large Food Manufacturer With High Seasonal Demand Semantic Scholar




Aggregate Planning Strategy Organization Levels System Examples Model Type Company System
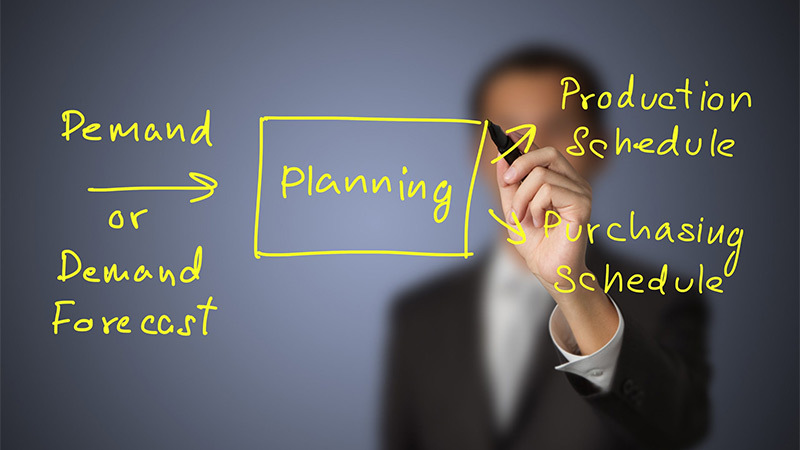



Capacity Planning An Industry Guide Plex Demandcaster



M Dc Operations Strategy
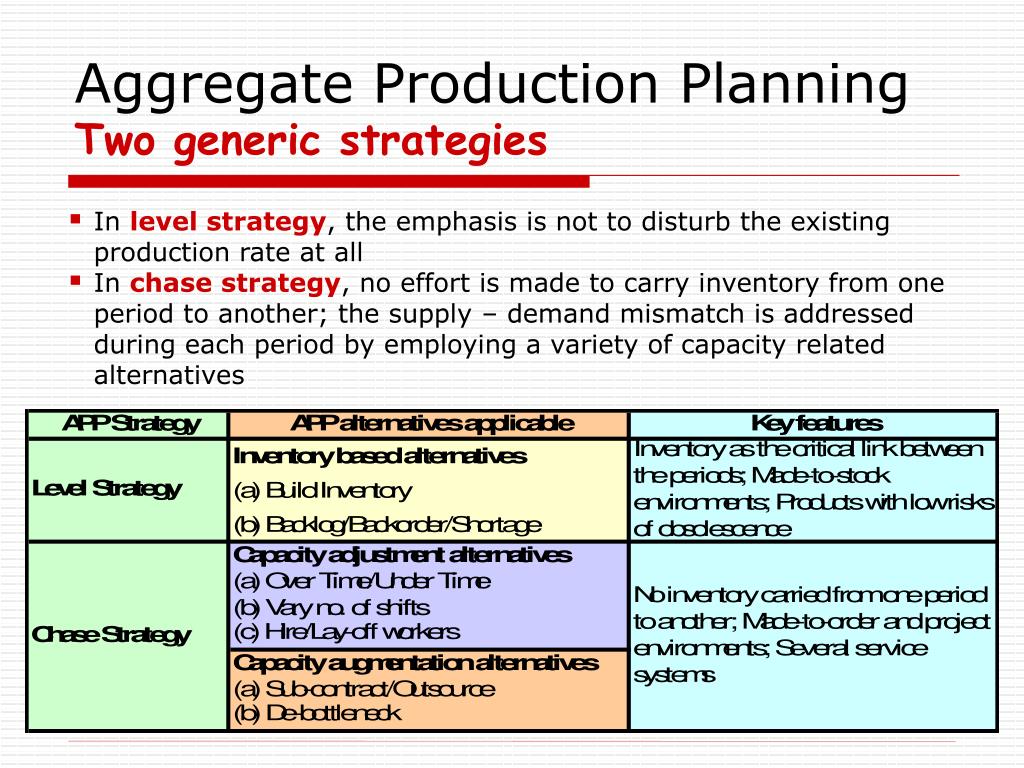



Ppt Aggregate Production Planning Powerpoint Presentation Free Download Id



1




Operations Management Chapter Multiple Choice Problems Flashcards Quizlet
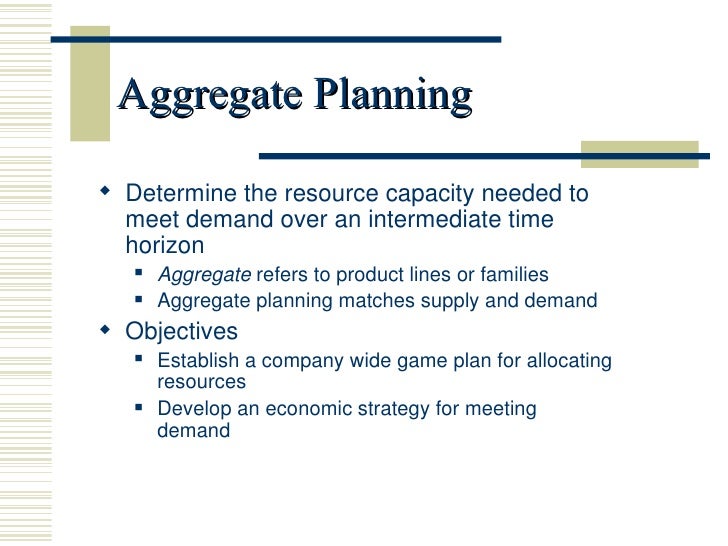



Aggregate Planning
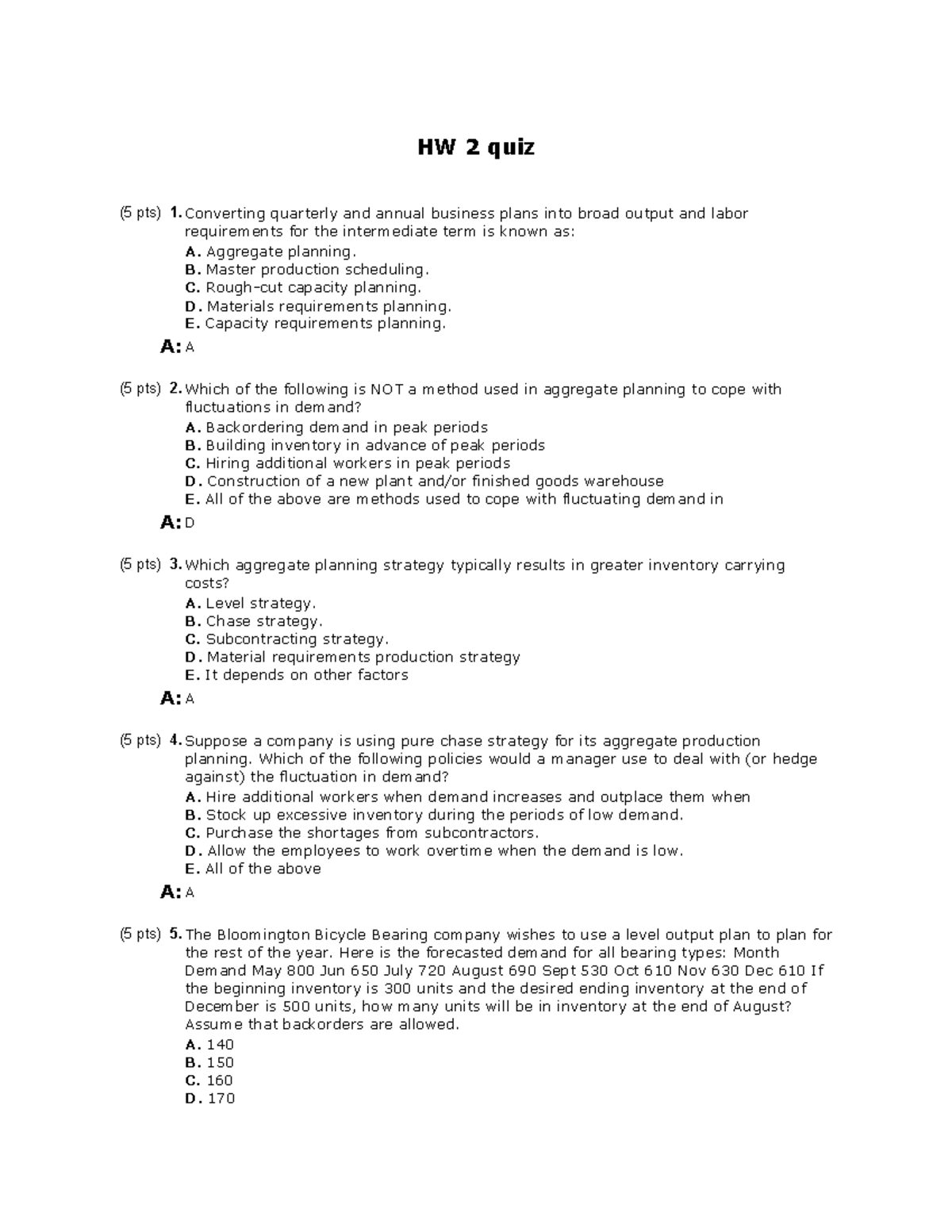



Hw2 Quiz With Answers Hw Quiz Pts Converting Quarterly And Annual Business Plans Into Broad Output And Labor Requirements For The Intermediate Term Is Known As Studocu



Inputs And Outputs To Aggregate Production Planning 4 Download Scientific Diagram
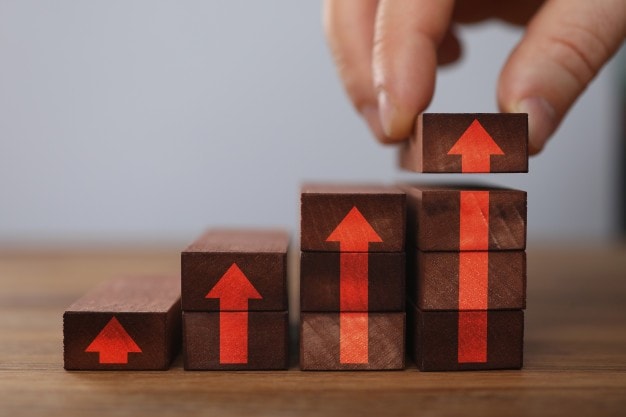



Aggregate Planning Definition Importance Strategies Management And Advantages
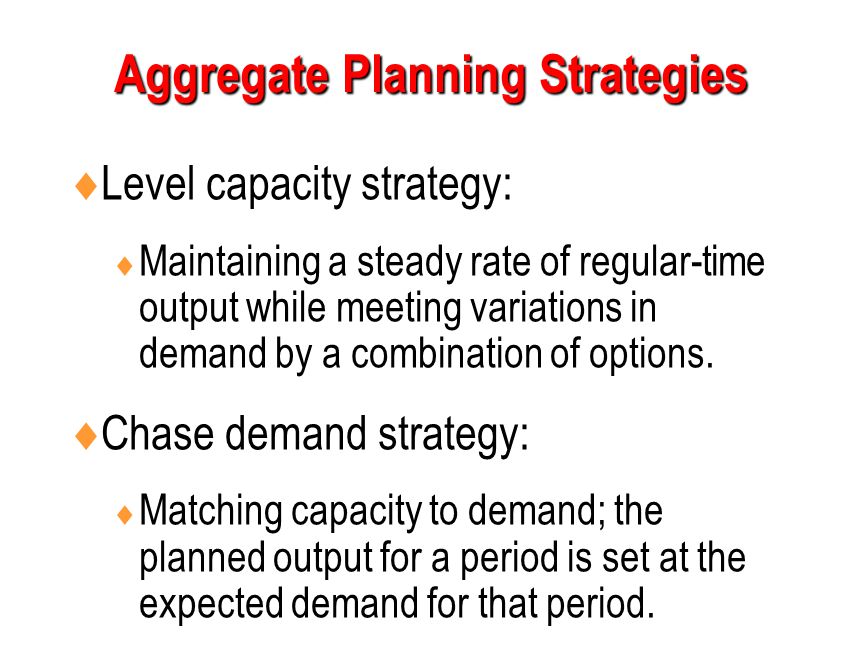



Aggregate Planning Ppt Download



Aggregate Planning In The Supply Chain Inventory Enterprise Resource Planning




Aggregate Planning Strategy Organization Levels System Examples Model Type Company System
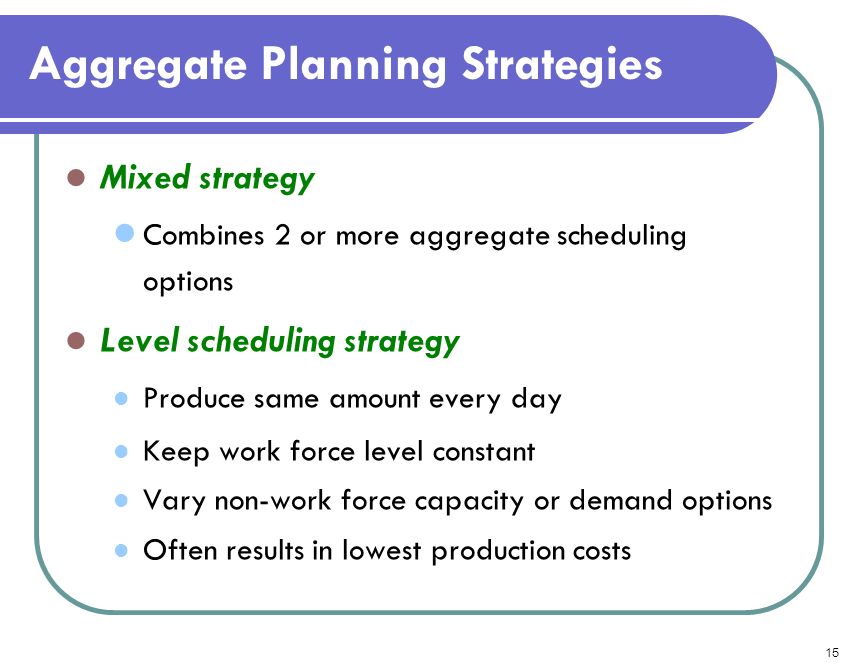



Operations Management Aggregate Planning Ppt Download



2
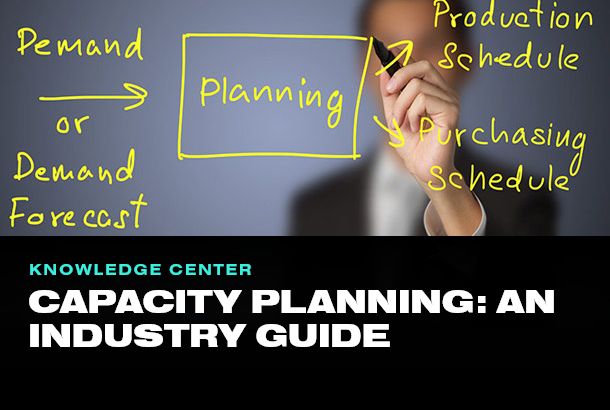



Capacity Planning An Industry Guide Plex Demandcaster
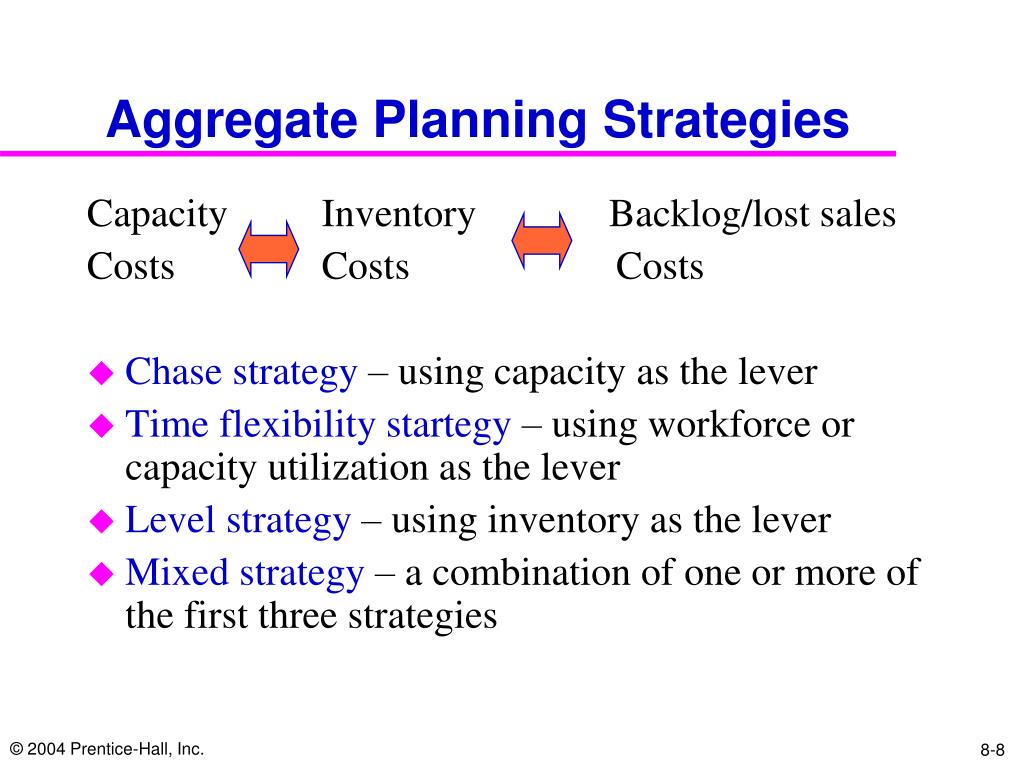



Ppt Chapter 8 Aggregate Planning In The Supply Chain Powerpoint Presentation Id
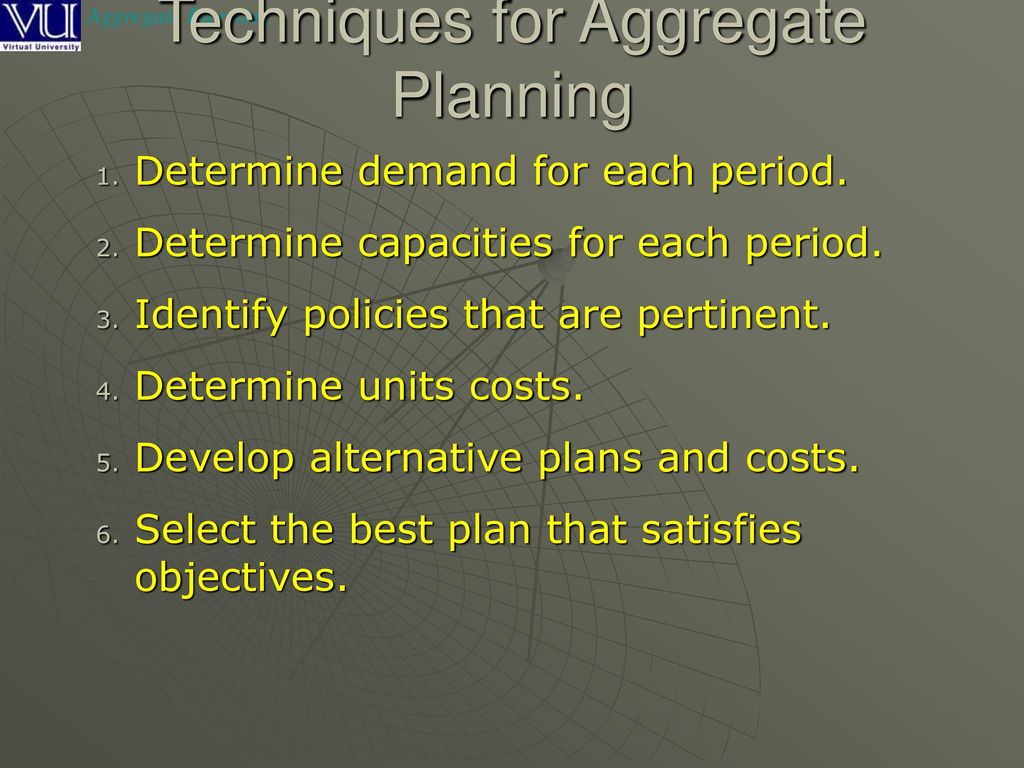



Basic Strategies Level Capacity Strategy Chase Demand Strategy Ppt Download




What Is Aggregate Planning A Comprehensive Look



Aggregate Production Planning Operations Management Homework And Assignment Help
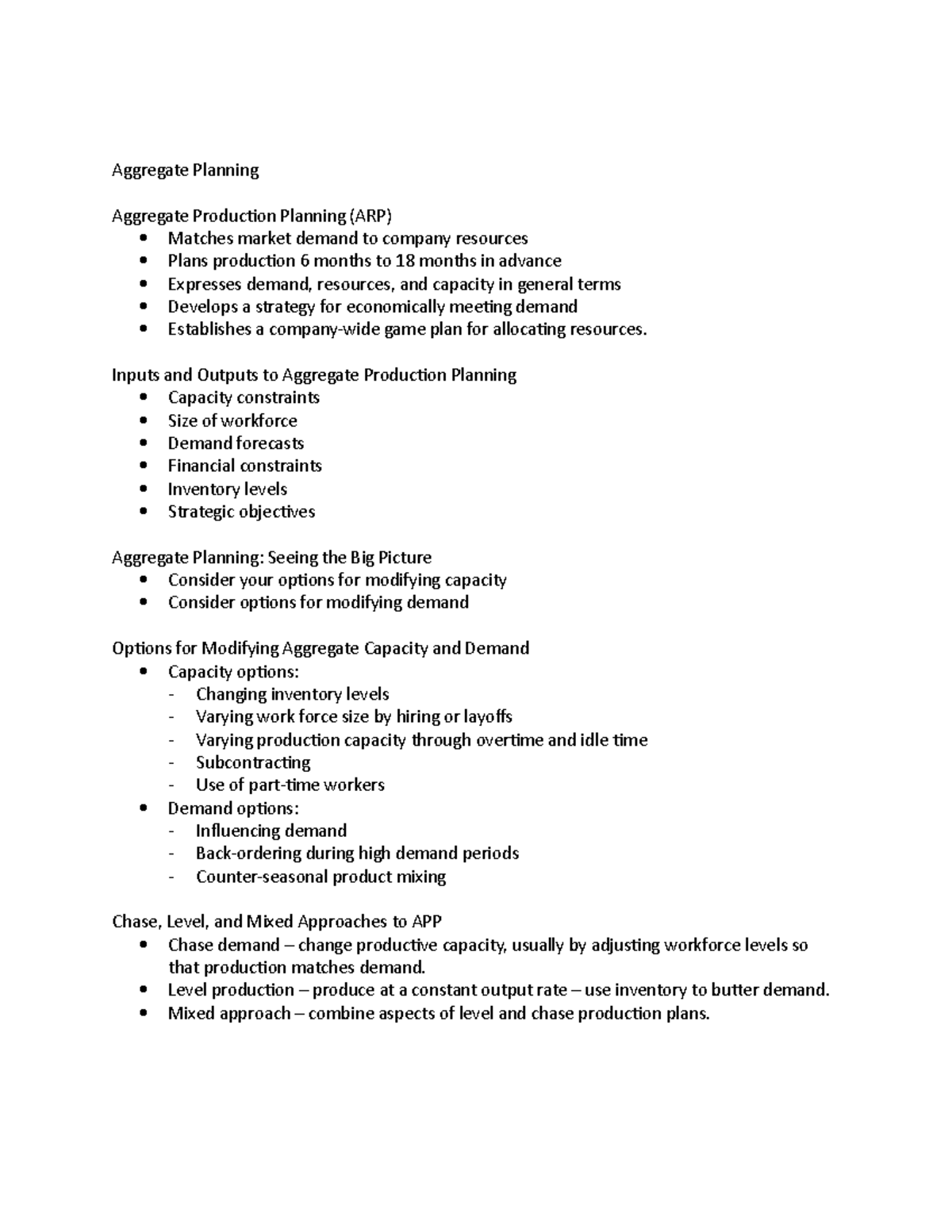



Aggregate Planning Lecture Notes 10 14 Studocu
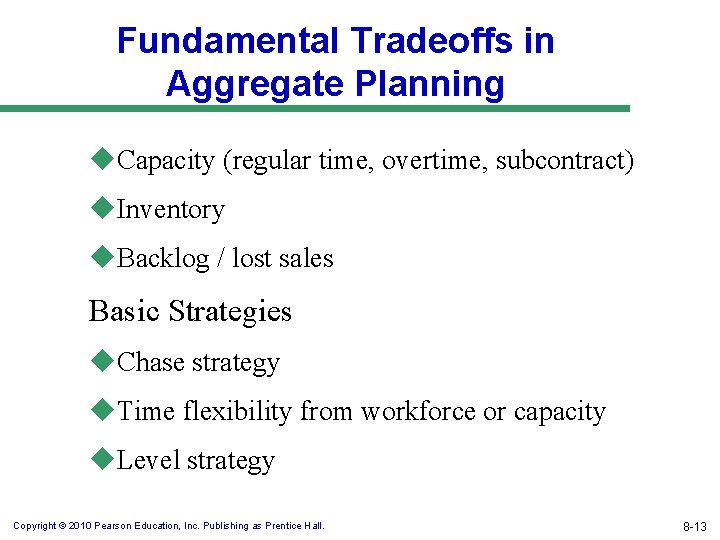



Chapter 8 Aggregate Planning In The Supply Chain
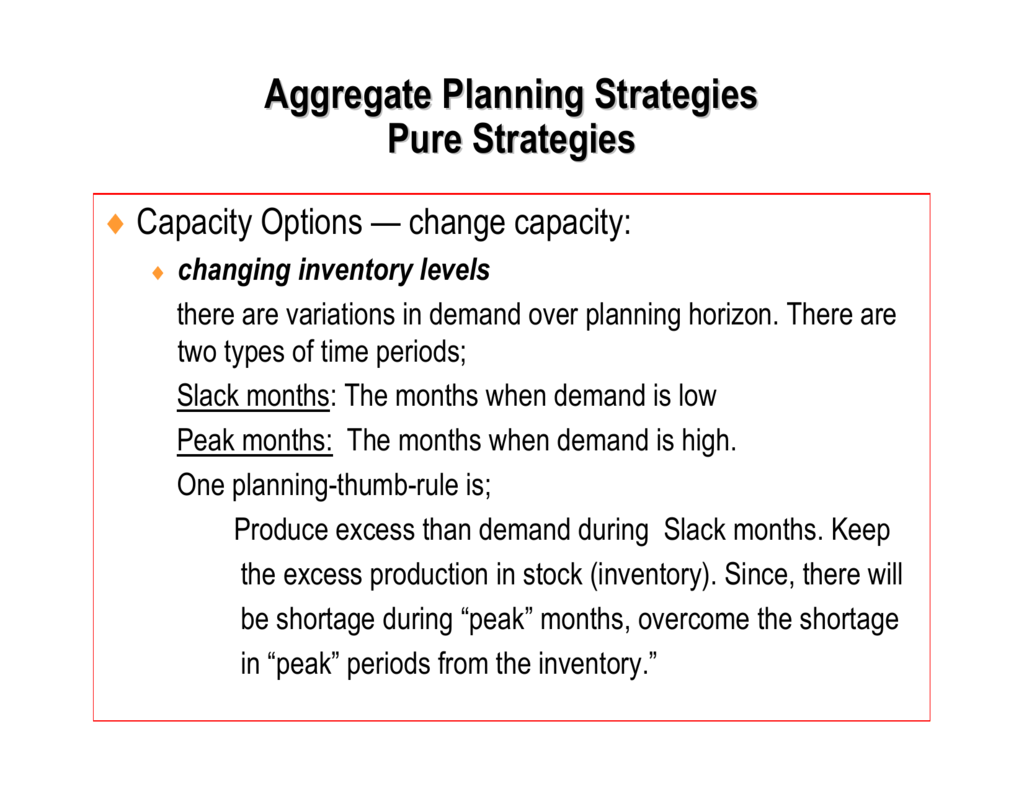



Aggregate Planning Strategies Pure Strategies
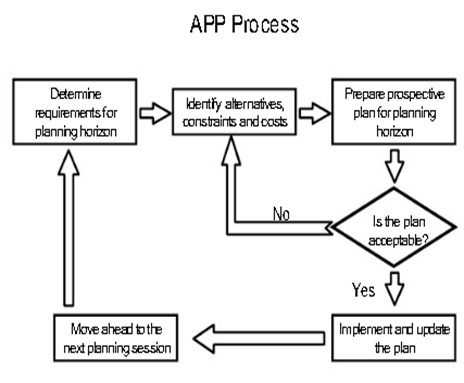



Aggregate Production Planning Aggregate Planning Process Aggregate Production Planning Strategies
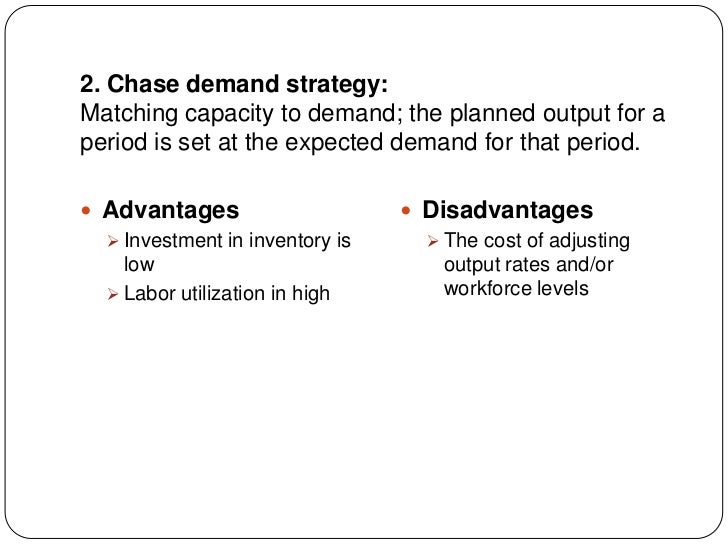



Aggregate Planning Report



Aggregate Planning Strategies Of Scm Inventory Demand



Http Www1 Pu Edu Tw Ylai Erp Dom 1042 Ppts S16 1042 Erp Dom Ap S16 Pdf
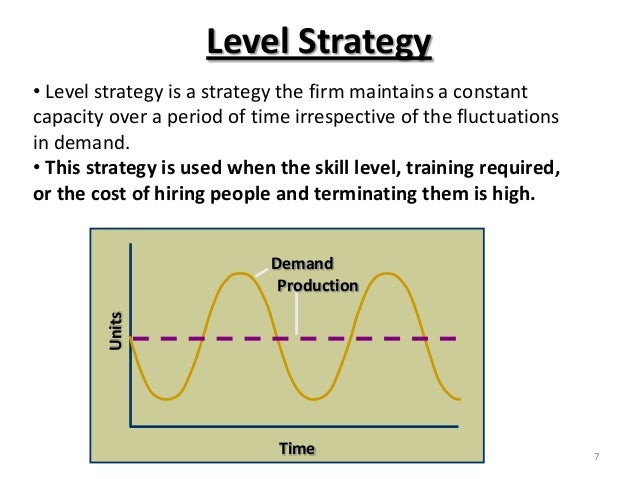



Models Of Aggregate Planning
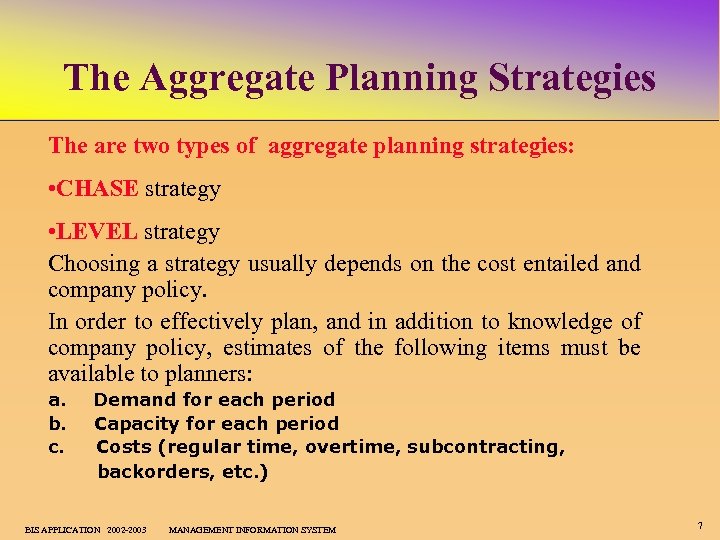



Aggregate Planning And Learning Curves Chapter Outline 1
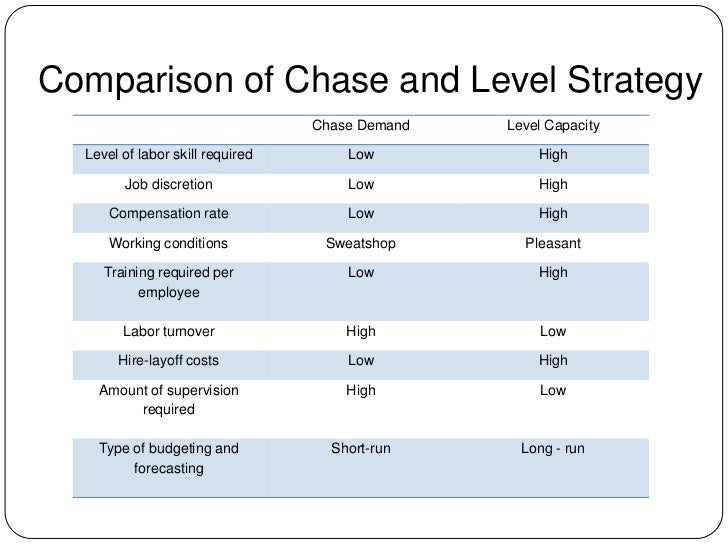



Aggregate Planning Report




Slides Show
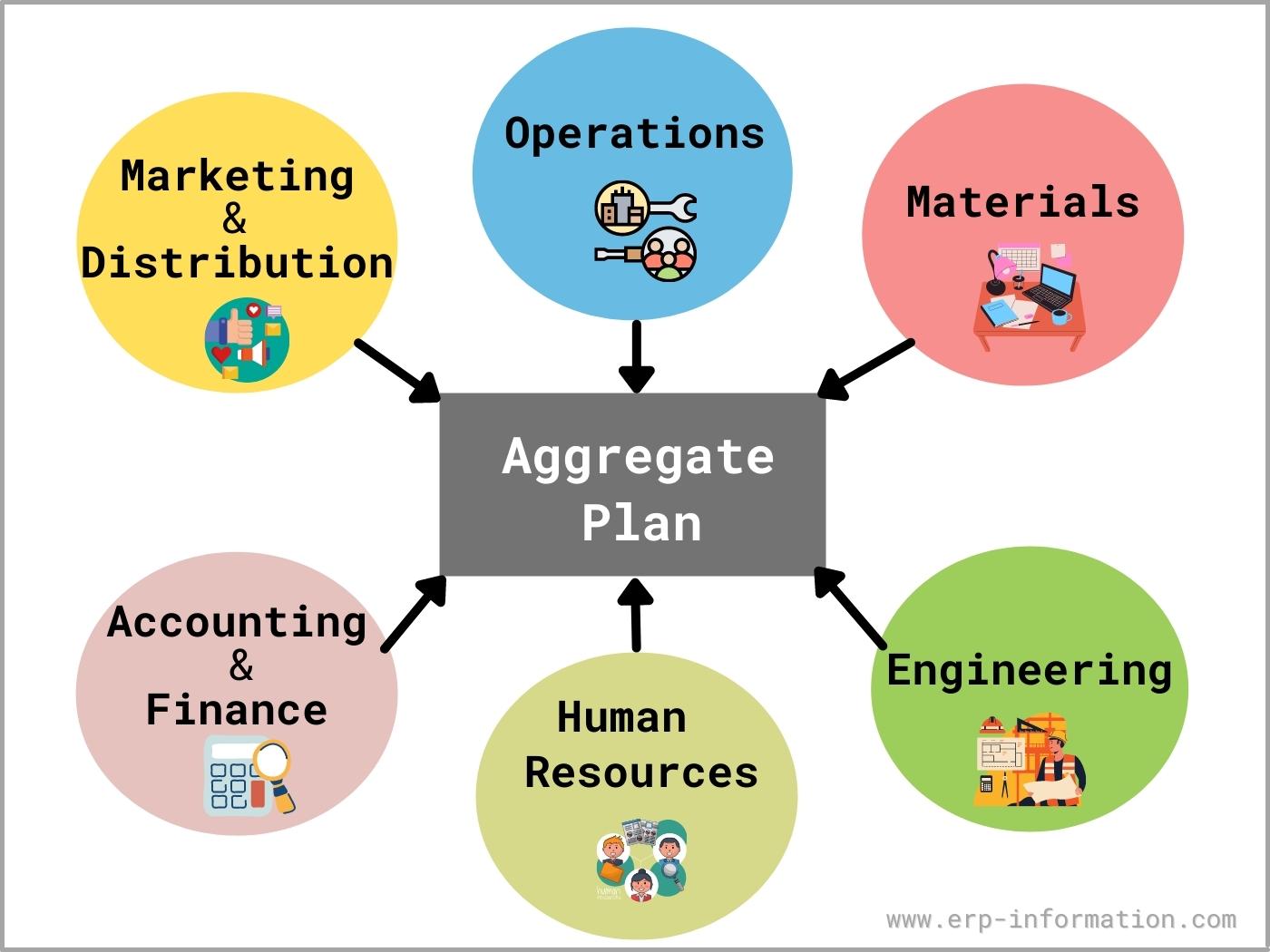



What Is Aggregate Planning 3 Strategies For Aggregate Production Planning




Capacity Planning Organization System Examples Definition System Long Term Capacity Planning




D Aggregate Planning Uses The Adjustable Part Of Capacity To Meet Production Course Hero
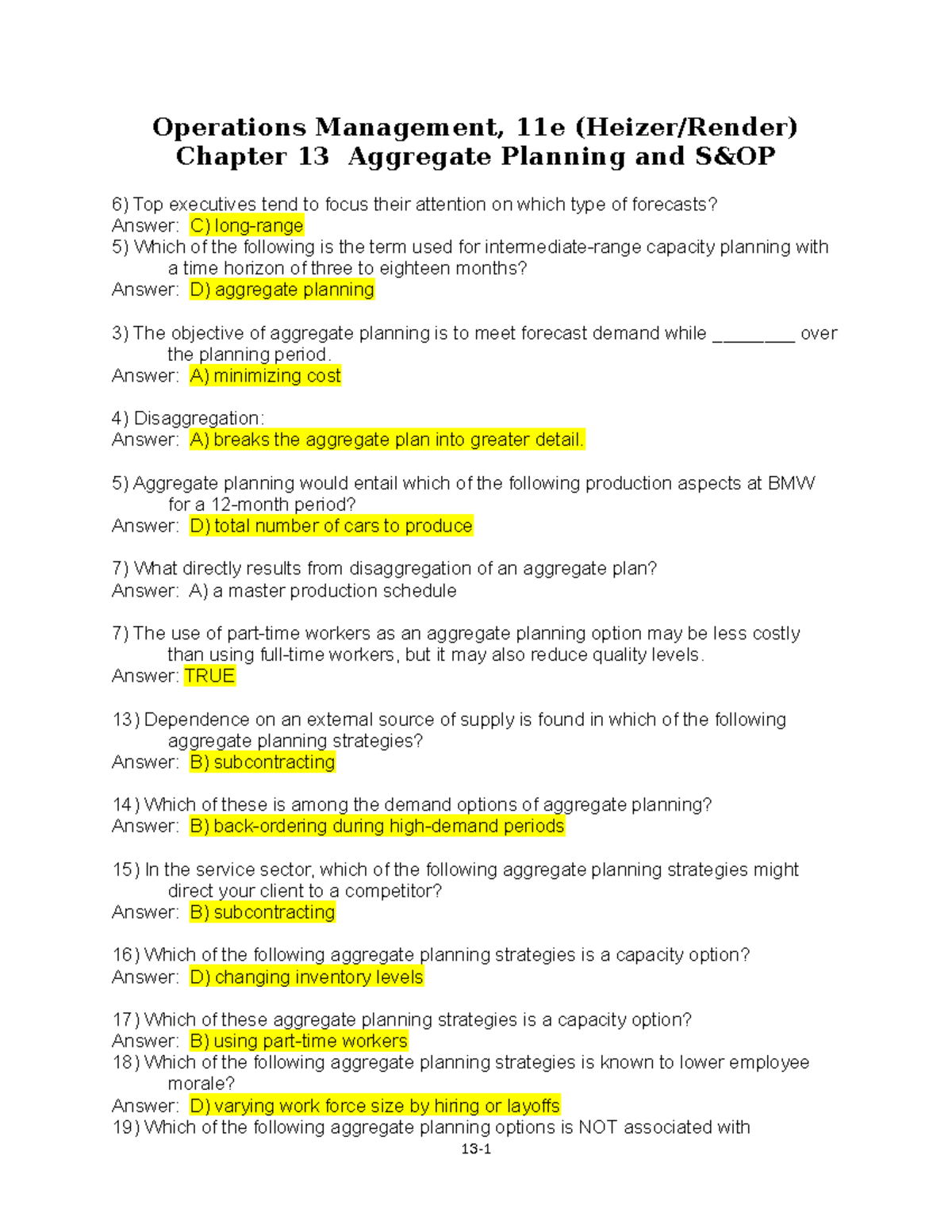



Mgt 3110 Chapter 13 Studocu



Larry Smith The Manager Of Cases For You Wants To Use Aggregate Planning For The Company S Line Of Rugged Carryon Suitcases Below Is The Company S Course Hero
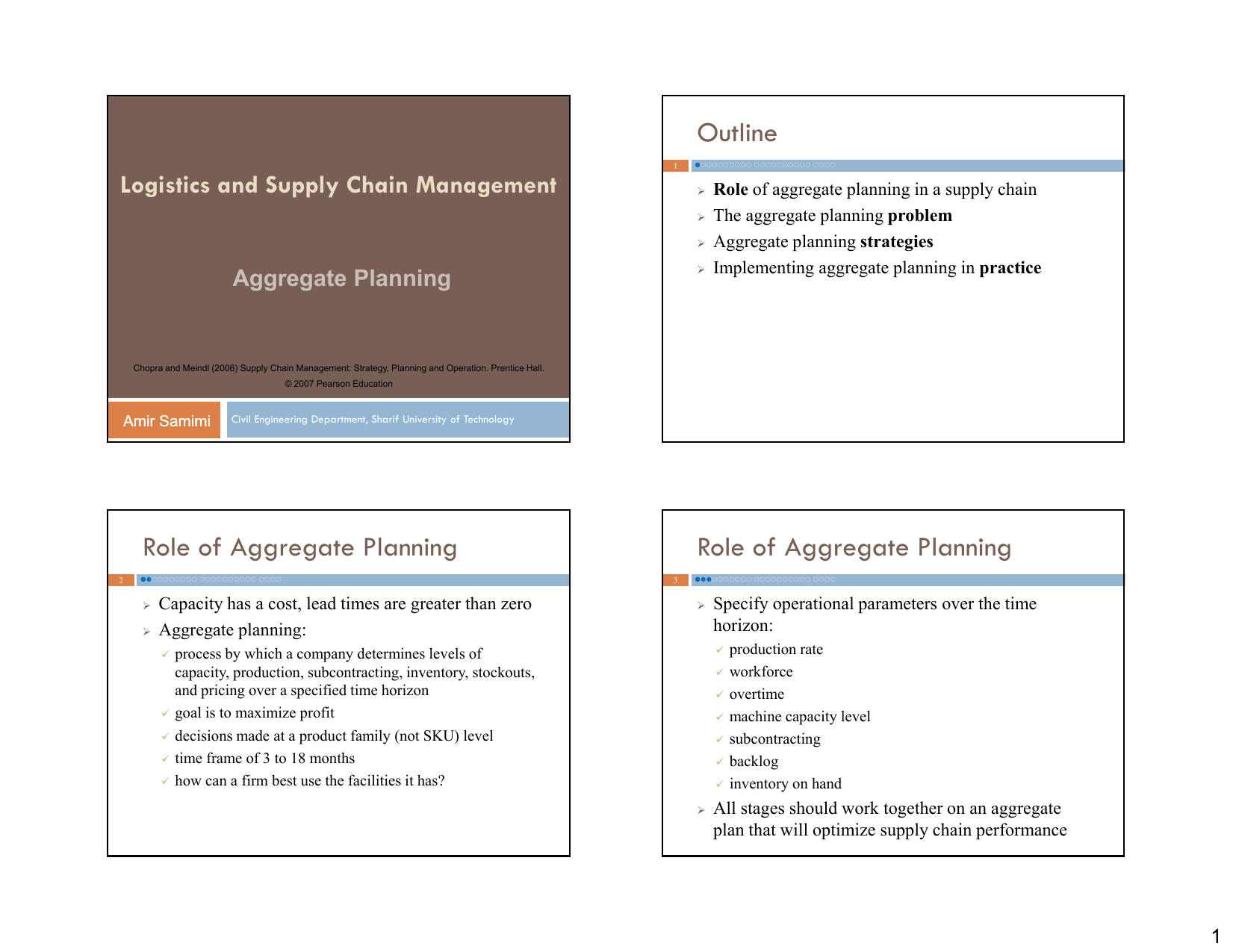



08




Aggregate Capacity Planning Pdf Free Download
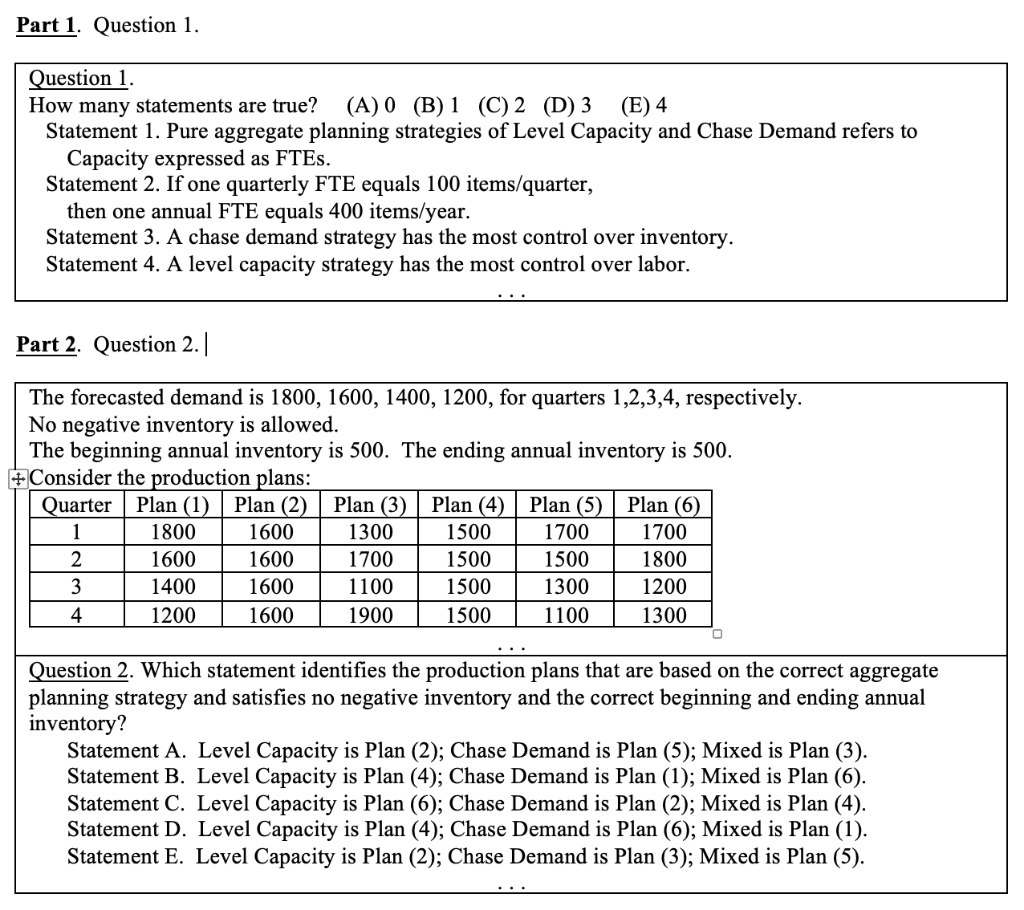



Part 1 Question 1 Question 1 How Many Statements Chegg Com
0 件のコメント:
コメントを投稿